Manual Sheet Bending Machine
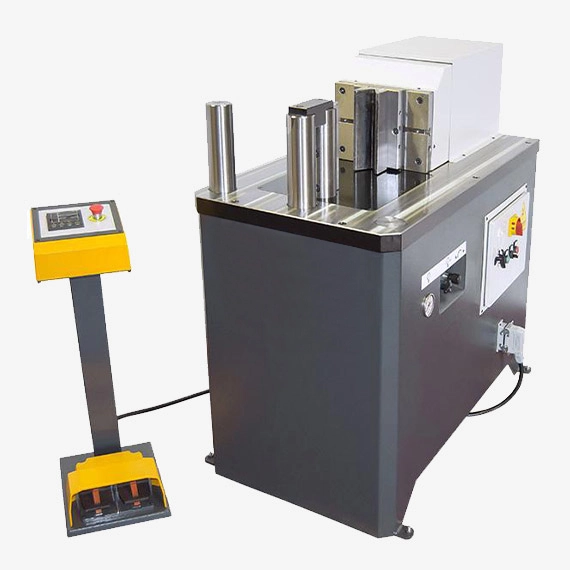
A manual sheet bending machine is a versatile tool used to shape sheet metal into various forms and angles by applying manual force. It is a common choice for small-scale workshops, hobbyists, and DIY projects due to its compact size, ease of use, and affordability.
Key Components of a Manual Sheet Bending Machine
- Frame: The frame provides a sturdy base for the machine and supports the bending mechanism. It is typically made from heavy-duty steel or cast iron.
- Bending Mechanism: The bending mechanism is the heart of the machine, applying the force required to bend the sheet metal. It consists of a bending form, a pressure roller, and a hand crank or lever. The bending form provides the desired shape, while the pressure roller applies force to bend the sheet metal, and the hand crank or lever transfers manual power to the bending mechanism.
- Work Table: The work table provides a stable surface for positioning and securing the sheet metal during bending. It may be adjustable to accommodate different sheet metal sizes and bending angles.
- Angle Indicator: The angle indicator allows the user to set the desired bending angle accurately.
- Controls: The controls allow the user to operate the machine, including setting the bending angle, engaging the bending mechanism, and controlling the speed of the bending process.
Common Applications of Manual Sheet Bending Machines
Manual sheet bending machines are suitable for various applications, including:
- Bending smaller to medium-sized sheet metal pieces (typically up to 1/8 inch or 3 mm)
- Creating prototype parts and small- to medium-scale production runs
- Forming ductwork, brackets, and other sheet metal components
- Manufacturing metal enclosures, cabinets, and other sheet metal products
- DIY projects and hobbyist applications
Benefits of Manual Sheet Bending Machines
Manual sheet bending machines offer several advantages over electric or hydraulic bending machines:
- Lower Cost: Manual machines are generally less expensive than electric or hydraulic machines, making them a more affordable option for small-scale operations.
- Ease of Use: Manual machines are relatively simple to operate and require minimal training, making them suitable for both experienced and novice users.
- Portability: Manual machines are typically smaller and lighter than electric or hydraulic machines, making them easier to transport and set up in various locations.
- Precision Control: Manual machines provide manual control over the bending process, allowing for precise adjustments and customization.
- Versatility: Manual machines can handle a variety of sheet metal materials, including mild steel, aluminum, copper, and brass.
Safety Precautions for Using Manual Sheet Bending Machines
When using manual sheet bending machines, it is essential to follow safety precautions to prevent injuries and accidents:
- Wear appropriate personal protective equipment (PPE): This includes safety glasses, gloves, and hearing protection.
- Secure the sheet metal before bending: The sheet metal should be firmly grasped and positioned correctly in the machine’s guides or rollers.
- Do not overload the machine: Overloading can damage the machine and cause injury.
- Keep hands away from moving parts: The bending mechanism and the workpiece can move unexpectedly, posing a hazard to hands.
- Avoid contact with energized components: Some manual machines may have electrical components that can cause electrical shock.
- Regular Maintenance: Follow a strict maintenance schedule to ensure the machine is in optimal condition and free of potential hazards.
By adhering to safety precautions and operating the machine properly, individuals can effectively shape sheet metal and create various components using manual sheet bending machines.
Manual Sheet Bending Machine
A horizontal hydraulic press machine is a powerful and versatile tool that utilizes hydraulic pressure to apply force horizontally to a workpiece. It is commonly used in various industries, including metalworking, manufacturing, and construction, for a wide range of applications such as bending, straightening, pressing, and forming.
Key Components of a Horizontal Hydraulic Press Machine
- Frame: The frame provides the structural backbone for the press, ensuring stability and rigidity during operation. It is typically constructed from heavy-duty steel plates or castings and is designed to withstand the high forces generated during pressing operations.
- Hydraulic Cylinder: The hydraulic cylinder is the heart of the press, converting hydraulic pressure into mechanical force. It consists of a piston, cylinder barrel, and hydraulic seals. The size of the cylinder determines the maximum force the press can exert.
- Hydraulic Pump and Power Unit: The hydraulic pump and power unit supply hydraulic fluid to the cylinder, generating the required pressure for operation. The pump draws fluid from a reservoir and forces it through a series of valves and filters into the cylinder. The power unit regulates the pressure and flow of hydraulic fluid.
- Control System: The control system manages the operation of the press, including ram movement, pressure control, and safety interlocks. It receives input from sensors, such as pressure transducers and position encoders, and controls the valves and actuators to regulate the press’s behavior.
- Ram: The ram is the movable part of the press that applies force directly to the workpiece. It is connected to the piston of the hydraulic cylinder and slides along guides within the frame. The ram can be equipped with various tooling, such as dies, punches, or adapters, depending on the specific application.
- Work Table or Bed: The work table or bed provides a stable surface for positioning and securing the workpiece during the pressing operation. It is typically adjustable to accommodate different workpiece sizes and heights.
- Tooling: Tooling is a crucial component of horizontal hydraulic press machines, allowing the press to perform various forming operations. Common tooling options include dies, punches, adapters, and forming tools. Dies are used to shape the workpiece, while punches are used to cut or pierce material. Adapters are used to connect different tooling components, and forming tools are used for specific forming operations, such as bending or straightening.
- Safety Interlocks: Safety interlocks are essential components that prevent hazardous situations from occurring during press operation. They typically include sensors that detect the presence of an operator or workpiece, and they prevent the press from activating if safety conditions are not met.
- Gauges and Indicators: Gauges and indicators provide the operator with real-time information about the press’s operation, such as hydraulic pressure, ram position, and press force. This information is crucial for monitoring the press’s performance and ensuring safe operation.
- Electrical System: The electrical system powers the control system, hydraulic pump, and other electrical components of the press. It includes wiring, electrical panels, and various electrical components, such as motors, relays, and switches.
Types of Horizontal Hydraulic Press Machines
Horizontal hydraulic press machines come in various types, each with its specific characteristics and applications:
- Single-acting Presses: These presses have a single hydraulic cylinder that applies force in one direction. They are suitable for simple bending and straightening operations.
- Double-acting Presses: These presses have two hydraulic cylinders, allowing for force application in both directions. They are more versatile and can handle a wider range of pressing operations.
- Four-column Presses: These presses feature four columns that provide exceptional stability and rigidity, making them suitable for heavy-duty applications.
- C-frame Presses: These presses have a C-shaped frame, offering a more compact design and suitable for smaller workpieces.
Applications of Horizontal Hydraulic Press Machines
Horizontal hydraulic press machines are versatile tools used for a wide range of applications in various industries:
- Metalworking: Bending, straightening, forming, and coining of metal components for manufacturing.
- Construction: Pressing and forming of sheet metal components for construction applications, such as roofing, cladding, and structural elements.
- Automotive Industry: Forming of automotive components, such as body panels, brackets, and structural parts.
- Aerospace Industry: Precision forming of aerospace components, ensuring high strength, dimensional accuracy, and structural integrity.
- Industrial Applications: Pressing and forming of various components for industrial machinery, equipment, and tools.
Safety Considerations for Horizontal Hydraulic Press Machine Operation
Safety is paramount when operating horizontal hydraulic press machines. Operators must follow strict safety guidelines to prevent accidents and injuries. These guidelines include:
- Wearing appropriate personal protective equipment (PPE), including safety glasses, gloves, and hearing protection.
- Ensuring proper machine setup and maintenance, following the manufacturer’s instructions.
- Securing the workpiece firmly on the work table before operation.
Metal Fabrication
Metal fabrication is the process of transforming raw metal materials into finished products through various manufacturing techniques and processes. It involves the manipulation, shaping, and assembly of metal components to create structures, machinery, equipment, and consumer goods for a wide range of industries.
Metal fabrication encompasses a diverse range of processes, including cutting, welding, bending, forming, machining, and finishing, each tailored to specific requirements and applications. From small-scale custom projects to large-scale industrial production, metal fabrication plays a vital role in manufacturing sectors such as construction, automotive, aerospace, electronics, and infrastructure development.
- Materials: Metal fabrication utilizes a variety of metals and alloys, including steel, aluminum, stainless steel, copper, brass, and titanium. The choice of material depends on factors such as strength, durability, corrosion resistance, and cost-effectiveness for the intended application.
- Cutting: Cutting is a fundamental process in metal fabrication, involving the removal of excess material to achieve desired shapes and dimensions. Common cutting methods include sawing, shearing, laser cutting, plasma cutting, waterjet cutting, and flame cutting, each suitable for different thicknesses and types of metal.
- Welding: Welding joins metal components together by melting and fusing them using heat, pressure, or a combination of both. Various welding techniques are used in metal fabrication, including MIG (Metal Inert Gas), TIG (Tungsten Inert Gas), stick welding, and flux-cored arc welding, each offering specific advantages in terms of strength, precision, and versatility.
- Bending and Forming: Bending and forming processes shape metal into desired geometries, such as angles, curves, and contours. Press brakes, roll forming machines, stamping presses, and tube benders are commonly used to bend and form metal components with precision and accuracy.
- Machining: Machining involves the removal of material from metal workpieces to achieve precise dimensions and surface finishes. Machining processes include milling, turning, drilling, grinding, and threading, performed using CNC (Computer Numerical Control) machines or conventional machining tools.
- Assembly: Assembly brings together individual metal components to create complete products or structures. Techniques such as welding, riveting, bolting, soldering, and adhesive bonding are used to join metal parts securely and reliably, ensuring structural integrity and functionality.
- Finishing: Finishing processes enhance the appearance, durability, and corrosion resistance of metal products. Surface treatments such as painting, powder coating, anodizing, plating, and polishing provide protective coatings and decorative finishes to metal surfaces, improving aesthetics and performance.
- Quality Control: Quality control measures are implemented throughout the metal fabrication process to ensure that finished products meet specified requirements and standards. Inspection, testing, and certification procedures verify dimensional accuracy, mechanical properties, and compliance with customer specifications and industry regulations.
Metal fabrication encompasses a wide range of specialized skills, technologies, and expertise, from design and engineering to manufacturing and assembly. It plays a critical role in modern industrial production, supplying essential components and structures for infrastructure, transportation, machinery, and consumer goods, driving innovation and economic growth in diverse sectors around the world.
Sheet Metal:
Sheet metal is a versatile material widely used in metal fabrication, manufacturing, and construction industries for various applications due to its flexibility, strength, and formability. It is characterized by its thinness, typically ranging from fractions of a millimeter to several millimeters in thickness, and is available in flat, thin sheets or coils.
- Material Composition: Sheet metal is primarily composed of ferrous and non-ferrous metals, including steel, aluminum, stainless steel, copper, brass, and titanium. Each material offers unique properties such as strength, corrosion resistance, conductivity, and ductility, making it suitable for specific applications.
- Thickness: Sheet metal thickness is specified by gauge, which represents the metal’s thickness relative to a standardized scale. Common gauge systems include the American Wire Gauge (AWG) for non-ferrous metals and the Standard Gauge (SWG) or Gauge (GA) system for ferrous metals. Thinner gauges correspond to thicker sheets, with lower gauge numbers indicating thicker metal.
- Formability: One of sheet metal’s key attributes is its formability, allowing it to be easily shaped, bent, and formed into complex geometries using various fabrication techniques. Sheet metal can undergo processes such as bending, folding, rolling, stretching, and deep drawing to create components with precise dimensions and contours.
- Manufacturing Processes: Sheet metal undergoes a range of manufacturing processes to achieve desired shapes, sizes, and properties. These processes include cutting (shearing, laser cutting, plasma cutting), bending (press braking, roll forming), forming (deep drawing, stamping), welding (MIG, TIG, spot welding), and finishing (painting, powder coating, plating).
- Applications: Sheet metal finds applications in numerous industries and products, including automotive bodies, aircraft fuselages, appliances, HVAC (heating, ventilation, and air conditioning) systems, electronics enclosures, architectural components, signage, and machinery parts. Its versatility, durability, and cost-effectiveness make it an ideal material for both functional and aesthetic purposes.
- Design Considerations: Designing with sheet metal requires careful consideration of factors such as material selection, thickness, geometry, and manufacturing processes. Design features such as flanges, bends, cutouts, and reliefs are incorporated to optimize structural integrity, manufacturability, and performance of sheet metal components.
- Cost Efficiency: Sheet metal fabrication is often preferred for its cost efficiency compared to other materials and manufacturing methods. Its relatively low material cost, high production speed, and recyclability make it a cost-effective choice for producing large quantities of components with consistent quality and performance.
- Environmental Impact: Sheet metal’s recyclability and sustainability contribute to its environmental benefits. Recycling scrap metal reduces the need for virgin metal production, conserves natural resources, and minimizes energy consumption and greenhouse gas emissions associated with metal extraction and processing, making sheet metal an eco-friendly choice for sustainable manufacturing practices.
In summary, sheet metal is a versatile and widely used material in metal fabrication, offering a combination of strength, formability, and cost-effectiveness for diverse applications across industries. Its properties, manufacturing processes, applications, design considerations, cost efficiency, and environmental impact make it an essential component of modern manufacturing and construction practices.
Welding:
Welding is a fundamental process in metal fabrication that joins two or more metal pieces together by melting and fusing them. It is a critical technique used across various industries, including automotive, aerospace, construction, and manufacturing, to create strong and durable metal structures and components.
- Principle of Welding: Welding works on the principle of metallurgical bonding, where the base metals are heated to their melting point, and a filler material is often added to facilitate fusion. As the molten metal cools, it solidifies, creating a strong and permanent joint between the welded parts.
- Welding Processes: There are several welding processes, each with its unique characteristics, applications, and advantages. Common welding processes include:
- MIG (Metal Inert Gas) Welding
- TIG (Tungsten Inert Gas) Welding
- Stick Welding (SMAW – Shielded Metal Arc Welding)
- Flux-Cored Arc Welding (FCAW)
- Submerged Arc Welding (SAW)
- Gas Metal Arc Welding (GMAW)
- Gas Tungsten Arc Welding (GTAW)
- Joint Preparation: Proper joint preparation is crucial for successful welding. It involves cleaning the base metals to remove dirt, rust, and contaminants that can weaken the weld. Additionally, the edges of the metal pieces may be beveled or chamfered to provide better penetration and fusion during welding.
- Welding Positions: Welding can be performed in various positions, depending on the orientation of the workpiece and the weld joint. Common welding positions include flat position, horizontal position, vertical position, and overhead position. Welders must adapt their technique to ensure proper weld penetration and deposition in each position.
- Welding Equipment: Welding equipment includes welding machines, electrodes, filler metals, shielding gases, welding torches, and safety gear such as welding helmets, gloves, and protective clothing. Welding machines provide the necessary electrical power to generate an arc, while electrodes and filler metals contribute to the weld pool formation and reinforcement.
- Welding Safety: Welding poses various hazards, including exposure to intense heat, UV radiation, fumes, and electrical shocks. Welders must follow strict safety protocols and wear appropriate personal protective equipment (PPE) to minimize the risk of injury or illness. Ventilation systems and welding screens are also used to control fume exposure and protect surrounding workers.
- Weld Quality Control: Quality control measures are essential to ensure the integrity and reliability of welded joints. Non-destructive testing (NDT) techniques, such as visual inspection, ultrasonic testing, radiographic testing, and dye penetrant testing, are used to detect defects, discontinuities, or imperfections in the welds without damaging the workpiece.
- Applications: Welding is used in a wide range of applications, including structural fabrication, pipeline construction, automotive manufacturing, shipbuilding, aerospace engineering, and repair and maintenance operations. It is essential for creating strong and durable connections in metal structures, machinery, equipment, and consumer goods.
In summary, welding is a versatile and indispensable process in metal fabrication, providing the means to create strong and reliable joints in metal components and structures. Its principles, processes, joint preparation, welding positions, equipment, safety considerations, quality control measures, and applications make it a cornerstone of modern manufacturing and construction industries.
Cutting:
Cutting is a fundamental process in metal fabrication that involves the removal of excess material to create desired shapes, dimensions, and features in metal workpieces. It is essential for preparing raw materials, shaping components, and separating parts during various fabrication operations.
- Cutting Methods: There are several methods used for cutting metal, each suited to different thicknesses, materials, and precision requirements. Common cutting methods include:
- Shearing: Shearing involves the use of sharp blades to cut through sheet metal by applying a shearing force along a straight line.
- Laser Cutting: Laser cutting utilizes a focused laser beam to melt, vaporize, or burn through metal, producing precise and intricate cuts.
- Plasma Cutting: Plasma cutting uses a high-velocity jet of ionized gas (plasma) to melt and remove metal from the workpiece.
- Waterjet Cutting: Waterjet cutting employs a high-pressure stream of water mixed with abrasive particles to erode and cut through metal.
- Flame Cutting: Flame cutting, also known as oxy-fuel cutting, uses a combination of oxygen and a fuel gas (acetylene, propane) to create a high-temperature flame that melts and cuts through metal.
- Cutting Parameters: Cutting parameters such as cutting speed, feed rate, depth of cut, and tool/material selection play a crucial role in determining the quality and efficiency of the cutting process. Optimal cutting parameters are selected based on factors such as material type, thickness, hardness, and desired cut quality.
- Precision Cutting: Precision cutting techniques, such as laser cutting and waterjet cutting, offer high accuracy and repeatability, making them suitable for intricate shapes, fine details, and tight tolerances. These methods minimize material waste and secondary processing steps, resulting in cost-effective production of precision components.
- Sheet Metal Cutting: Sheet metal cutting is a common application of cutting processes, where thin metal sheets are cut to size and shape for various fabrication projects. Shearing, laser cutting, and plasma cutting are commonly used for sheet metal cutting due to their speed, versatility, and ability to produce clean edges.
- Thick Metal Cutting: Cutting thick metal poses challenges due to increased material density, heat absorption, and cutting forces. Methods such as plasma cutting, flame cutting, and waterjet cutting are preferred for thick metal cutting, as they provide sufficient cutting power and penetration to handle thick materials effectively.
- Heat Affected Zone (HAZ): Cutting processes that generate heat, such as laser cutting and plasma cutting, can create a heat-affected zone (HAZ) along the cut edge. The HAZ may exhibit changes in material properties, such as hardness, microstructure, and residual stress, which can affect the performance of the cut part.
- Cutting Safety: Cutting operations involve potential hazards, including sharp edges, flying debris, heat, and noise. Operators must follow safety protocols and wear appropriate personal protective equipment (PPE), such as safety glasses, gloves, and hearing protection, to minimize the risk of injury.
- Advanced Cutting Technologies: Advances in cutting technologies, such as CNC (Computer Numerical Control) cutting machines and automated cutting systems, have revolutionized metal fabrication by enabling precise, efficient, and repeatable cutting operations. CNC programming allows for complex cutting patterns and shapes to be executed with high speed and accuracy, enhancing productivity and flexibility in fabrication processes.
In summary, cutting is a critical process in metal fabrication, essential for shaping, sizing, and preparing metal workpieces for further fabrication operations. Its various methods, parameters, applications, safety considerations, and advancements contribute to the efficiency, precision, and quality of metal cutting operations in diverse industrial sectors.
Forming:
Forming is a metal fabrication process that involves shaping and manipulating metal workpieces into desired geometries, contours, and dimensions. It is essential for creating complex parts and components with specific shapes and functionalities across various industries.
- Types of Forming Processes: Forming encompasses a wide range of processes, each suited to different materials, shapes, and production requirements. Common forming processes include:
- Bending: Bending involves deforming metal workpieces along a straight axis to create angles, curves, or bends. Press brakes, roll forming machines, and tube benders are commonly used for bending operations.
- Stretching: Stretch forming stretches metal sheets or profiles over a die to achieve elongated shapes or contours. It is commonly used in automotive body panel manufacturing and aircraft fuselage production.
- Deep Drawing: Deep drawing involves forming metal blanks into three-dimensional shapes using a punch and die set. It is used to produce cylindrical or box-shaped parts, such as cans, containers, and automotive body panels.
- Roll Forming: Roll forming gradually shapes metal strips or coils into continuous profiles by passing them through a series of rollers. It is commonly used for producing structural shapes, such as beams, channels, and tubes.
- Spinning: Spinning, or metal spinning, involves rotating a metal disc or tube against a forming tool to shape it into a symmetrical or axisymmetric part. It is used to produce cylindrical or conical shapes, such as cookware, lampshades, and satellite dishes.
- Material Considerations: Forming processes can be performed on various metals and alloys, including steel, aluminum, stainless steel, copper, brass, and titanium. The choice of material depends on factors such as strength, ductility, formability, and desired properties of the finished part.
- Tooling and Equipment: Forming operations require specialized tooling and equipment designed to exert controlled forces and deformation on metal workpieces. Tooling includes dies, punches, rollers, mandrels, and molds, which are customized to the specific shapes and dimensions of the desired parts.
- Forming Limits: Each forming process has its limitations in terms of the shapes, sizes, and complexities of parts that can be produced. Understanding material properties, deformation behavior, and forming mechanics is essential to avoid defects such as wrinkling, tearing, cracking, or springback during forming operations.
- Precision and Accuracy: Precision forming techniques, such as CNC bending, roll forming, and hydroforming, offer high accuracy and repeatability, making them suitable for producing parts with tight tolerances and intricate features. Advanced control systems and automation further enhance precision and efficiency in forming processes.
- Applications: Forming is used in various industries and applications to produce a wide range of parts and components, including automotive body panels, aerospace structures, household appliances, HVAC ductwork, architectural elements, and consumer products. Its versatility, efficiency, and flexibility make it indispensable in modern manufacturing.
- Forming Safety: Forming operations involve potential hazards such as pinch points, entanglement, and material ejection. Operators must follow safety protocols and use appropriate personal protective equipment (PPE), such as gloves, safety glasses, and hearing protection, to minimize the risk of injury.
- Advanced Forming Technologies: Advances in forming technologies, such as incremental forming, hydroforming, electromagnetic forming, and additive manufacturing (3D printing), have expanded the capabilities of traditional forming processes, enabling the production of complex shapes, lightweight structures, and customized parts with greater efficiency and flexibility.
In summary, forming is a versatile and essential process in metal fabrication, enabling the creation of complex and customized parts with specific shapes and functionalities. Its various processes, material considerations, tooling and equipment, precision and accuracy, applications, safety considerations, and advancements contribute to the efficiency, quality, and innovation in modern manufacturing industries.
Machining:
Machining is a metal fabrication process that involves the removal of material from a workpiece to achieve desired shapes, dimensions, and surface finishes. It encompasses a wide range of techniques and operations performed using machine tools, such as lathes, milling machines, drills, and grinders, to produce precise and complex metal components.
- Types of Machining Operations: Machining encompasses various operations, each suited to specific geometries, features, and tolerances required for the final part. Common machining operations include:
- Turning: Turning involves rotating a workpiece against a cutting tool to remove material and create cylindrical shapes, such as shafts, pins, and spindles.
- Milling: Milling uses rotary cutters to remove material from a workpiece, producing flat surfaces, slots, pockets, and complex contours. It is versatile and widely used for producing prismatic parts, molds, and dies.
- Drilling: Drilling creates holes in a workpiece using rotary cutting tools called drills. It is essential for producing holes of various sizes and depths in metal components.
- Grinding: Grinding uses abrasive wheels to remove material from a workpiece’s surface, achieving precise dimensions and surface finishes. It is used for finishing operations and for producing tight tolerances and smooth surfaces.
- Boring: Boring enlarges existing holes or produces cylindrical features with high accuracy and concentricity. It is commonly used in machining cylinders, engine blocks, and gear housings.
- Broaching: Broaching uses a specialized tool called a broach to remove material in a linear motion, producing keyways, splines, and other internal profiles in workpieces.
- Sawing: Sawing cuts metal workpieces using saw blades, producing straight or contoured cuts. It is used for cutting bars, tubes, and structural shapes in metal fabrication.
- Machine Tools: Machining operations are performed using various machine tools and equipment, including:
- Lathes: Used for turning cylindrical or conical shapes.
- Milling Machines: Used for milling flat surfaces and complex shapes.
- Drilling Machines: Used for drilling holes in workpieces.
- Grinding Machines: Used for grinding surfaces and producing fine finishes.
- CNC Machines: Computer Numerical Control (CNC) machines automate machining processes, allowing for precise and complex machining operations with high repeatability and efficiency.
- Tooling: Machining requires a variety of cutting tools, tool holders, fixtures, and workholding devices to hold and manipulate workpieces during machining operations.
- Material Considerations: Machining can be performed on a wide range of metals and alloys, including steel, aluminum, stainless steel, copper, brass, titanium, and exotic alloys. The choice of material depends on factors such as strength, hardness, machinability, and desired properties of the finished part.
- Precision and Tolerance: Machining offers high precision and tight tolerances, making it suitable for producing parts with critical dimensions and geometric features. CNC machining allows for precise control of cutting parameters, tool paths, and part orientation, ensuring consistent quality and accuracy in machined components.
- Surface Finishing: Machining operations can produce a variety of surface finishes, ranging from rough to mirror-like finishes, depending on machining parameters and tooling selection. Finishing processes such as grinding, polishing, and deburring are often employed to improve surface quality and remove machining marks.
- Applications: Machining is used in various industries and applications to produce a wide range of components and parts, including automotive engine components, aerospace structures, medical devices, consumer electronics, and precision instruments. Its versatility, precision, and flexibility make it indispensable in modern manufacturing.
- Machining Safety: Machining operations involve potential hazards such as rotating machinery, flying chips, and sharp cutting tools. Operators must follow safety protocols and use appropriate personal protective equipment (PPE), such as safety glasses, gloves, and hearing protection, to minimize the risk of injury.
- Advanced Machining Technologies: Advances in machining technologies, such as multi-axis machining, high-speed machining, and additive manufacturing (3D printing), have expanded the capabilities of traditional machining processes, enabling the production of complex shapes, lightweight structures, and customized parts with greater efficiency and flexibility.
In summary, machining is a versatile and essential process in metal fabrication, offering precise and efficient means of producing complex and customized metal components. Its various operations, machine tools, material considerations, precision and tolerance, surface finishing, applications, safety considerations, and advancements contribute to the efficiency, quality, and innovation in modern manufacturing industries.
Stamping:
Stamping is a metal fabrication process that involves the shaping or forming of metal sheets or coils using a press and dies. It is a versatile and cost-effective manufacturing method used to produce high volumes of parts with consistent quality and precision.
- Principle of Stamping: Stamping works on the principle of applying mechanical force to deform metal sheets or coils between a press and a die set. The die set consists of a male (punch) and female (die) component, which shape the metal into the desired geometry by shearing, bending, drawing, or stretching.
- Types of Stamping Operations: Stamping encompasses various operations, each suited to different part geometries and production requirements. Common stamping operations include:
- Blanking: Cutting flat shapes or profiles from sheet metal using a punch and die set.
- Piercing: Creating holes, slots, or openings in sheet metal using a punch and die set.
- Bending: Forming metal into angles, curves, or shapes using a press brake or bending die.
- Drawing: Stretching or pulling metal into three-dimensional shapes using a punch and die set.
- Coining: Producing fine details, embossing, or texturing on metal surfaces using a press and specialized dies.
- Progressive Die Stamping: Performing multiple stamping operations in sequence using a progressive die set, allowing for high-speed and automated production of complex parts.
- Materials: Stamping can be performed on various metals and alloys, including steel, aluminum, stainless steel, copper, brass, and titanium. The choice of material depends on factors such as strength, ductility, formability, and desired properties of the finished part.
- Stamping Equipment: Stamping operations are performed using mechanical or hydraulic presses equipped with dies, feed systems, and automation components. Presses range in size from small benchtop models to large industrial machines capable of exerting hundreds or thousands of tons of force.
- Tooling: Stamping tooling consists of punch and die sets designed to produce specific part geometries and features. Tooling materials may include tool steel, carbide, or specialized coatings to withstand the forces and wear associated with stamping operations.
- Precision and Tolerance: Stamping offers high precision and tight tolerances, making it suitable for producing parts with consistent dimensions and intricate features. Advanced tooling design, press controls, and monitoring systems ensure accurate and repeatable stamping processes.
- Applications: Stamping is used in various industries and applications to produce a wide range of parts and components, including automotive body panels, appliance enclosures, electronic enclosures, hardware fittings, aerospace components, and consumer products. Its high-speed production capabilities and cost-effectiveness make it ideal for mass production of stamped parts.
- Stamping Safety: Stamping operations involve potential hazards such as pinch points, entanglement, and flying debris. Operators must follow safety protocols and use appropriate personal protective equipment (PPE), such as safety glasses, gloves, and hearing protection, to minimize the risk of injury.
- Environmental Considerations: Stamping generates scrap material and waste during the production process. Recycling programs and waste reduction strategies help minimize environmental impact by reclaiming scrap metal and optimizing material usage.
In summary, stamping is a versatile and efficient metal fabrication process used to produce high volumes of precision parts with consistent quality and performance. Its various operations, materials, equipment, tooling, precision and tolerance, applications, safety considerations, and environmental considerations contribute to its widespread use in modern manufacturing industries.
Assembly:
Assembly is a crucial phase in metal fabrication that involves joining individual metal components or parts together to create complete assemblies, sub-assemblies, or finished products. It encompasses a range of techniques and processes to securely and accurately connect metal parts, ensuring structural integrity, functionality, and performance.
- Joining Methods: Assembly utilizes various methods to join metal parts, each suited to different materials, geometries, and assembly requirements. Common joining methods include:
- Welding: Welding joins metal parts by melting and fusing them together using heat and pressure. Techniques such as MIG welding, TIG welding, spot welding, and seam welding are used to create strong and permanent bonds between metal components.
- Mechanical Fastening: Mechanical fasteners such as bolts, screws, nuts, rivets, and clips are used to secure metal parts together. Fasteners provide reliable connections that allow for disassembly and reassembly, making them suitable for applications requiring maintenance or repair.
- Adhesive Bonding: Adhesive bonding uses adhesives or bonding agents to bond metal parts together. Adhesives provide uniform distribution of stress, seal joints against moisture or contaminants, and dampen vibrations, making them ideal for lightweight or non-ferrous materials.
- Clinching: Clinching is a cold-forming process that joins metal parts by deforming them under high pressure. It creates interlocking features such as tabs, flanges, or grooves, which mechanically lock the parts together without additional fasteners or adhesives.
- Press-Fit Assembly: Press-fit assembly involves inserting one metal part into another with an interference fit, creating a tight, frictional connection between the mating surfaces. It is commonly used in automotive, electronics, and machinery applications.
- Soldering and Brazing: Soldering and brazing use filler metals with lower melting points to join metal parts together. These processes create strong, leak-tight connections suitable for joining dissimilar metals or heat-sensitive components.
- Assembly Techniques: Assembly techniques vary depending on the complexity, size, and design of the metal components being joined. Techniques such as manual assembly, automated assembly, robotic assembly, and fixture-based assembly are used to ensure accurate alignment, fitment, and assembly sequence.
- Fixturing and Tooling: Fixturing and tooling are essential for holding and positioning metal parts during assembly operations. Jigs, fixtures, clamps, and alignment tools ensure precise alignment and orientation of parts, facilitating efficient and accurate assembly processes.
- Quality Control: Quality control measures are implemented throughout the assembly process to ensure that finished assemblies meet specified requirements and standards. Inspection, testing, and verification procedures verify dimensional accuracy, fitment, functionality, and compliance with customer specifications.
- Lean Manufacturing Principles: Lean manufacturing principles such as 5S (Sort, Set in order, Shine, Standardize, Sustain), Kanban, and continuous improvement (Kaizen) are applied to optimize assembly processes, minimize waste, reduce cycle times, and improve productivity and efficiency.
- Automation and Robotics: Automation and robotics play an increasingly important role in metal assembly, offering advantages such as higher throughput, repeatability, and accuracy. Automated assembly systems, robotic arms, vision systems, and motion control technologies enhance productivity and flexibility in assembly operations.
- Environmental Considerations: Assembly processes may generate waste, emissions, or energy consumption that impact the environment. Sustainable practices such as waste reduction, recycling, energy efficiency, and pollution prevention help minimize the environmental footprint of assembly operations.
- Worker Safety: Assembly operations involve potential hazards such as sharp edges, moving parts, heavy lifting, and exposure to chemicals or fumes. Workers must follow safety protocols and use appropriate personal protective equipment (PPE) to minimize the risk of injury or illness.
In summary, assembly is a critical phase in metal fabrication that brings together individual metal components to create functional and durable assemblies or products. Its various joining methods, assembly techniques, fixturing and tooling, quality control measures, lean manufacturing principles, automation and robotics, environmental considerations, and worker safety practices ensure efficient, reliable, and sustainable assembly processes in modern manufacturing industries.
Finishing:
Finishing is a crucial step in metal fabrication that involves surface treatment, coating, or post-processing of metal parts to enhance their appearance, durability, corrosion resistance, and functionality. It adds value to metal components and ensures they meet desired aesthetic and performance standards.
- Surface Preparation: Surface preparation is essential before applying any finishing treatment to metal parts. It involves cleaning, degreasing, and removing contaminants such as rust, scale, oil, or dirt from the surface to ensure proper adhesion and uniform coating application.
- Surface Treatment Techniques: Finishing techniques vary depending on the desired surface properties and requirements of the metal parts. Common surface treatment techniques include:
- Painting: Painting involves applying a layer of paint or coating to metal surfaces to provide color, protection, and decorative finishes. Various painting methods such as spray painting, powder coating, and electrostatic painting are used to achieve different coating thicknesses, textures, and appearances.
- Plating: Plating, also known as electroplating, involves depositing a thin layer of metal (e.g., chromium, nickel, zinc) onto metal surfaces through electrochemical processes. Plating enhances corrosion resistance, wear resistance, and aesthetic appeal, as well as providing decorative finishes such as chrome plating or gold plating.
- Anodizing: Anodizing is an electrochemical process that creates a protective oxide layer on the surface of aluminum or other non-ferrous metals. Anodized coatings provide corrosion resistance, abrasion resistance, and improved adhesion for dyes or paints, as well as decorative finishes in various colors.
- Passivation: Passivation removes free iron or iron oxide from the surface of stainless steel through chemical treatment, forming a passive oxide layer that enhances corrosion resistance. Passivated surfaces are often used in medical devices, food processing equipment, and aerospace components.
- Mechanical Finishing: Mechanical finishing techniques such as sanding, grinding, polishing, and buffing are used to remove surface imperfections, burrs, or scratches, and to achieve desired surface textures, smoothness, or reflectivity.
- Thermal Finishing: Thermal finishing processes such as heat treatment, flame treatment, or thermal spraying modify the surface properties of metal parts through controlled heating or cooling. These processes improve hardness, wear resistance, or adhesion of surface coatings.
- Customization and Branding: Finishing processes offer opportunities for customization and branding of metal parts to reflect company logos, product names, or other identifying marks. Laser engraving, embossing, or etching techniques are commonly used to imprint designs or text onto metal surfaces.
- Functional Coatings: In addition to aesthetic enhancements, finishing processes may include functional coatings or treatments to impart specific properties to metal parts. These coatings may provide lubrication, corrosion protection, abrasion resistance, thermal insulation, or electrical conductivity, depending on the application requirements.
- Quality Control: Quality control measures ensure that finished metal parts meet specified requirements and standards for appearance, performance, and durability. Visual inspection, measurement, adhesion testing, and accelerated aging tests verify the quality and integrity of surface finishes.
- Environmental Considerations: Finishing processes may involve the use of chemicals, solvents, or energy-intensive equipment that can impact the environment. Sustainable practices such as using low-VOC (volatile organic compound) coatings, water-based paints, or eco-friendly treatments help minimize environmental impact and comply with regulations.
- Cost Considerations: Finishing adds to the overall cost of metal fabrication due to the additional materials, labor, and equipment required for surface treatment. Cost-effective finishing solutions balance aesthetic and functional requirements with production efficiency and cost constraints.
In summary, finishing is a critical aspect of metal fabrication that enhances the appearance, durability, and functionality of metal parts. Its various surface treatment techniques, customization options, functional coatings, quality control measures, environmental considerations, and cost factors contribute to the overall quality and value of finished metal components in diverse industries.
Quality Control:
Quality control is an integral aspect of metal fabrication that ensures products meet specified standards, requirements, and customer expectations. It encompasses a range of processes, procedures, and techniques to monitor, evaluate, and improve the quality of metal parts throughout the fabrication process.
- Quality Management Systems (QMS): Quality control begins with the establishment of a comprehensive quality management system (QMS) that defines quality objectives, procedures, and responsibilities within the organization. QMS frameworks such as ISO 9001 provide guidelines for implementing effective quality management practices.
- Quality Planning: Quality planning involves defining quality objectives, requirements, and criteria for each stage of the fabrication process. It includes identifying critical quality parameters, setting inspection points, and developing quality control plans to ensure compliance with standards and specifications.
- Incoming Material Inspection: Quality control starts with the inspection of incoming raw materials, components, or supplies to verify their quality, conformity, and suitability for use in fabrication processes. Material testing, dimensional inspection, and certification verification are performed to ensure compliance with specifications.
- In-Process Inspection: In-process inspection involves monitoring and verifying the quality of metal parts at various stages of fabrication, from cutting and forming to welding and assembly. Inspection procedures, checklists, and visual inspections are conducted to detect defects, deviations, or non-conformities early in the process.
- Dimensional Metrology: Dimensional metrology techniques such as calipers, micrometers, gauges, and coordinate measuring machines (CMMs) are used to measure and verify the dimensional accuracy and tolerances of metal parts. Precision measurements ensure parts meet design requirements and functional specifications.
- Non-Destructive Testing (NDT): Non-destructive testing methods such as ultrasonic testing, radiographic testing, magnetic particle testing, and dye penetrant testing are used to detect defects, discontinuities, or imperfections in metal parts without causing damage. NDT techniques ensure the integrity and reliability of fabricated components.
- Welding Inspection: Welding inspection involves evaluating weld quality, penetration, and integrity to ensure welded joints meet specified standards and performance requirements. Visual inspection, welder qualification testing, and destructive testing are performed to verify weld quality and compliance with welding procedures.
- Traceability and Documentation: Quality control includes establishing traceability systems to track the production history, material sources, and inspection records of metal parts. Documentation of quality records, inspection reports, certificates of compliance, and traceability logs ensures transparency and accountability in the fabrication process.
- Corrective and Preventive Actions (CAPA): Quality control identifies deviations, non-conformities, or quality issues through inspections, audits, or customer feedback. Corrective and preventive actions are implemented to address root causes, prevent recurrence, and continuously improve quality performance.
- Continuous Improvement: Quality control is a continuous process of monitoring, analyzing, and improving quality performance throughout the organization. Feedback mechanisms, data analysis, and performance metrics are used to identify opportunities for improvement and drive continuous quality enhancement efforts.
In summary, quality control is essential in metal fabrication to ensure that products meet quality standards, specifications, and customer requirements. Its various aspects, including quality planning, inspection, dimensional metrology, non-destructive testing, welding inspection, traceability, corrective actions, and continuous improvement, contribute to the consistent delivery of high-quality metal components in diverse industries.
Material Selection:
Material selection is a critical aspect of metal fabrication that involves choosing the most suitable metals or alloys for specific applications based on their properties, performance requirements, and environmental conditions. Proper material selection ensures the durability, functionality, and cost-effectiveness of fabricated components.
- Properties Consideration: Material selection begins with an understanding of the desired properties and performance requirements of the fabricated components. Key properties to consider include:
- Mechanical Properties: Strength, hardness, ductility, toughness, and fatigue resistance influence the structural integrity and load-bearing capacity of metal parts.
- Thermal Properties: Thermal conductivity, thermal expansion, and heat resistance affect the ability of metal parts to withstand temperature variations and thermal stresses.
- Corrosion Resistance: Resistance to corrosion, oxidation, and chemical attack is crucial for components exposed to harsh environments or corrosive substances.
- Electrical Conductivity: Electrical conductivity and resistivity determine the suitability of metals for electrical and electronic applications.
- Magnetic Properties: Magnetic permeability and coercivity influence the magnetic behavior and compatibility of metal parts in electromagnetic systems.
- Wear Resistance: Wear resistance, frictional properties, and surface hardness are important for components subjected to abrasive wear, sliding contact, or impact.
- Material Types: A wide range of metals and alloys are available for metal fabrication, each with unique properties and characteristics. Commonly used materials include:
- Steel: Steel is a versatile and widely used metal alloy known for its strength, durability, and affordability. Different grades of steel offer varying levels of hardness, corrosion resistance, and machinability, making them suitable for a wide range of applications.
- Aluminum: Aluminum alloys are lightweight, corrosion-resistant, and have excellent thermal and electrical conductivity. They are used in industries such as aerospace, automotive, and construction where weight savings and durability are important.
- Stainless Steel: Stainless steel offers superior corrosion resistance, strength, and hygienic properties, making it ideal for applications in the food processing, medical, and chemical industries.
- Copper: Copper is valued for its high electrical conductivity, thermal conductivity, and malleability. It is used in electrical wiring, heat exchangers, plumbing, and architectural applications.
- Brass: Brass is an alloy of copper and zinc known for its attractive appearance, machinability, and corrosion resistance. It is used in decorative hardware, fittings, musical instruments, and plumbing fixtures.
- Material Compatibility: Material compatibility is essential when selecting metals for applications involving contact with other materials, chemicals, or environmental conditions. Compatibility considerations include galvanic corrosion, chemical reactions, thermal expansion coefficients, and mechanical interactions between dissimilar materials.
- Environmental Factors: Environmental factors such as temperature, humidity, UV exposure, and atmospheric pollutants can affect the performance and longevity of metal components. Materials resistant to environmental degradation, such as stainless steel or corrosion-resistant alloys, are preferred for outdoor or harsh environment applications.
- Cost Considerations: Material selection involves balancing performance requirements with cost considerations to achieve the desired balance of functionality, durability, and affordability. Factors such as material availability, processing costs, maintenance requirements, and lifecycle costs are taken into account when evaluating material options.
- Regulatory Compliance: Compliance with industry standards, regulations, and specifications is essential when selecting materials for applications in regulated industries such as aerospace, automotive, medical, and food processing. Materials must meet specific performance, safety, and quality requirements to ensure regulatory compliance and product reliability.
In summary, material selection is a crucial decision in metal fabrication that impacts the performance, durability, and cost-effectiveness of fabricated components. Considerations such as properties, material types, compatibility, environmental factors, cost, and regulatory compliance guide the selection process to ensure the optimal choice of materials for each application.
Sheet Metal Fabrication:
Sheet metal fabrication is a manufacturing process that involves shaping, cutting, and forming thin metal sheets into desired shapes and structures. It is widely used in various industries for producing components and assemblies with precise dimensions, complex geometries, and high strength-to-weight ratios.
- Raw Material: Sheet metal fabrication begins with the selection of raw materials, typically metal sheets or coils, which are available in various grades, thicknesses, and sizes. Commonly used materials include steel, aluminum, stainless steel, copper, and brass, each offering unique properties and characteristics suited to different applications.
- Cutting: Cutting is the initial step in sheet metal fabrication, where metal sheets are cut into specific shapes or sizes using various cutting techniques. Common cutting methods include:
- Shearing: Shearing uses a shear blade to cut metal sheets along straight lines, producing clean and precise edges.
- Laser Cutting: Laser cutting employs a focused laser beam to melt or vaporize metal material, achieving high accuracy and intricate cuts.
- Plasma Cutting: Plasma cutting uses a plasma torch to cut through metal sheets by generating a high-temperature plasma arc.
- Waterjet Cutting: Waterjet cutting uses a high-pressure jet of water mixed with abrasive particles to cut through metal sheets, offering versatility and minimal heat-affected zones.
- Forming and Bending: Forming and bending operations shape metal sheets into desired contours, angles, or geometries. Common forming techniques include:
- Bending: Bending uses a press brake or bending machine to deform metal sheets along straight axes, creating bends, angles, or curves.
- Roll Forming: Roll forming gradually shapes metal sheets or strips by passing them through a series of rollers, producing continuous profiles or complex shapes.
- Stretch Forming: Stretch forming stretches metal sheets over a die to form three-dimensional shapes or contours, commonly used in aerospace and automotive industries.
- Stamping and Punching: Stamping and punching operations create holes, cutouts, or features in metal sheets using punches and dies. These operations include:
- Blanking: Blanking cuts flat shapes or profiles from metal sheets, leaving the desired part shape as the finished product.
- Piercing: Piercing creates holes, slots, or openings in metal sheets using a punch and die set, often used for fastener installation or component assembly.
- Embossing: Embossing raises or depresses metal surfaces to create decorative patterns, logos, or textures, enhancing aesthetic appeal or functional properties.
- Welding and Joining: Welding and joining techniques are used to assemble multiple metal components or sheets into larger structures or assemblies. Common welding methods include:
- MIG Welding: Metal Inert Gas (MIG) welding uses a consumable wire electrode and inert gas shield to create strong and durable welds.
- TIG Welding: Tungsten Inert Gas (TIG) welding uses a non-consumable tungsten electrode and inert gas shield, producing high-quality welds with precise control.
- Spot Welding: Spot welding applies localized heat and pressure to join overlapping metal sheets together, commonly used in automotive and appliance manufacturing.
- Finishing: Finishing operations such as deburring, grinding, polishing, and coating are performed to improve the surface finish, appearance, and durability of fabricated metal parts. Surface treatments such as painting, plating, anodizing, or powder coating provide corrosion resistance, aesthetic appeal, and functional properties.
- Quality Control: Quality control measures ensure that fabricated metal parts meet specified requirements and standards for dimensions, tolerances, surface finish, and mechanical properties. Inspection, testing, and verification procedures are conducted throughout the fabrication process to detect defects, deviations, or non-conformities.
In summary, sheet metal fabrication is a versatile and essential manufacturing process used to produce a wide range of components and assemblies for various industries. Its cutting, forming, stamping, welding, finishing, and quality control operations enable the efficient and cost-effective production of high-quality metal parts with precise dimensions and complex geometries.
CNC Machining:
Computer Numerical Control (CNC) machining is a versatile manufacturing process used to create precise and complex metal components through automated machining operations. It involves the use of computer-controlled machine tools to remove material from a workpiece to achieve desired shapes, dimensions, and surface finishes.
- CAD/CAM Design: CNC machining begins with the creation of a digital 3D model of the desired part using Computer-Aided Design (CAD) software. The CAD model is then converted into machine-readable instructions using Computer-Aided Manufacturing (CAM) software, which generates toolpaths and machining strategies for the CNC machine.
- Workpiece Preparation: The workpiece, typically a block or bar of metal, is securely mounted onto the CNC machine’s worktable or fixture. Fixturing ensures proper alignment and stability during machining operations, minimizing vibration and deflection.
- Tool Selection: CNC machining employs a variety of cutting tools, such as end mills, drills, taps, reamers, and inserts, to remove material from the workpiece. Tool selection depends on factors such as material type, part geometry, cutting forces, and surface finish requirements.
- Machining Operations: CNC machining encompasses a range of machining operations, including:
- Milling: Milling operations remove material from the workpiece using rotating cutting tools (end mills) to create features such as slots, pockets, contours, and complex surfaces.
- Turning: Turning operations rotate the workpiece while a stationary cutting tool (lathe tool) removes material to create cylindrical or conical shapes, such as shafts, rods, and bushings.
- Drilling: Drilling operations create holes in the workpiece using rotating drill bits to achieve precise diameters, depths, and positional accuracy.
- Tapping: Tapping operations thread holes in the workpiece using specialized taps to create internal threads for fasteners or fittings.
- CNC Control System: The CNC machine is controlled by a computerized control system that interprets the CAM-generated toolpaths and sends commands to the machine’s motors and actuators. The control system coordinates the movement of the machine’s axes (X, Y, Z) and adjusts cutting parameters such as spindle speed, feed rate, and depth of cut.
- Accuracy and Precision: CNC machining offers high accuracy and precision, with the ability to achieve tight tolerances and fine surface finishes. Advanced CNC machines incorporate linear encoders, ball screws, and servo drives to minimize errors and ensure repeatability in machining operations.
- Multi-Axis Machining: Some CNC machines feature multiple axes of motion, allowing for more complex machining operations and simultaneous machining of multiple surfaces. Multi-axis machining enables the production of intricate geometries, contours, and freeform shapes with fewer setups and tool changes.
- Post-Processing: After machining, the finished parts may undergo additional post-processing operations such as deburring, polishing, heat treatment, or surface coating to improve their appearance, functionality, or performance.
- Quality Control: Quality control measures, including dimensional inspection, surface roughness measurement, and material testing, ensure that machined parts meet specified requirements and standards. CNC machines may incorporate in-process monitoring and feedback systems to detect errors and deviations during machining operations.
- Versatility and Efficiency: CNC machining is highly versatile and adaptable to a wide range of materials, including metals, plastics, and composites. It offers flexibility in production, allowing for rapid prototyping, small-batch production, and high-volume manufacturing with minimal setup time and labor costs.
In summary, CNC machining is a sophisticated manufacturing process that combines computer programming, precision machining, and automation to produce complex metal components with high accuracy, repeatability, and efficiency. Its versatility, accuracy, precision, and efficiency make it an indispensable technology in modern manufacturing industries.
Waterjet Cutting:
Waterjet cutting is a versatile and precise metal fabrication process that utilizes a high-pressure jet of water mixed with abrasive particles to cut through various materials. It offers several advantages, including the ability to cut intricate shapes, tight tolerances, and minimal material waste.
- Principle of Operation: Waterjet cutting works by forcing a stream of pressurized water, typically in the range of 30,000 to 90,000 psi (2,000 to 6,200 bar), through a small orifice at the nozzle. Abrasive particles, such as garnet or aluminum oxide, are added to the water stream to increase cutting efficiency and abrasive power. The high-speed abrasive-laden water jet erodes the material, creating a narrow kerf and achieving precise cuts.
- Materials: Waterjet cutting is suitable for cutting a wide range of materials, including metals, plastics, composites, ceramics, glass, stone, and foam. It can effectively cut through materials of varying thicknesses, densities, and hardness levels, making it a versatile choice for many applications.
- Advantages:
- Precision: Waterjet cutting offers high precision and accuracy, with the ability to achieve intricate shapes, tight tolerances (typically ±0.005 inches or 0.13 mm), and sharp corners without heat-affected zones or distortion.
- Versatility: Waterjet cutting is suitable for cutting a wide variety of materials, including reflective metals, heat-sensitive materials, and brittle materials, which may be difficult to cut using other methods.
- Minimal Material Waste: Waterjet cutting produces minimal material waste due to its narrow kerf width and the ability to nest parts closely together on the material sheet, optimizing material utilization and reducing costs.
- No Heat Affected Zone (HAZ): Unlike thermal cutting methods such as laser cutting or plasma cutting, waterjet cutting does not generate heat during the cutting process, minimizing the risk of thermal distortion, warping, or metallurgical changes in the material.
- Environmentally Friendly: Waterjet cutting is an environmentally friendly process that uses water as the primary cutting medium and does not produce hazardous fumes, dust, or by-products. The abrasive particles can be recycled, further reducing waste.
- Applications:
- Aerospace: Waterjet cutting is used in the aerospace industry for cutting complex shapes and components from aluminum, titanium, and composite materials used in aircraft structures and interiors.
- Automotive: Waterjet cutting is employed in the automotive industry for cutting gaskets, seals, interior trim, and custom parts from materials such as rubber, plastic, and foam.
- Architectural: Waterjet cutting is utilized in architectural applications for cutting decorative panels, floor tiles, countertops, and intricate metal designs from materials such as stone, glass, and metal.
- Manufacturing: Waterjet cutting is widely used in manufacturing for cutting machine parts, prototypes, tooling, and production components from various metals, plastics, and composites.
- Artistic: Waterjet cutting is popular in artistic and creative industries for cutting sculptures, signage, artwork, and custom designs from a variety of materials with precision and detail.
- Limitations:
- Speed: Waterjet cutting may not be as fast as some other cutting methods, such as laser cutting or plasma cutting, especially for thicker materials or complex geometries.
- Cost: The initial investment cost for waterjet cutting equipment may be higher compared to other cutting methods, although operational costs can be lower due to reduced material waste and minimal tooling wear.
- Edge Quality: While waterjet cutting produces clean and precise edges, the surface finish may not be as smooth as other cutting methods, requiring additional finishing operations if a smoother surface is desired.
In summary, waterjet cutting is a versatile and precise metal fabrication process suitable for cutting a wide range of materials and geometries with high precision, minimal material waste, and environmental sustainability. Its applications span various industries, from aerospace and automotive to architectural and artistic, making it a valuable technology in modern manufacturing and design.
Laser Cutting:
Laser cutting is a highly precise and versatile metal fabrication process that uses a focused laser beam to cut through various materials. It offers several advantages, including high accuracy, speed, and the ability to cut intricate shapes with minimal material waste.
- Principle of Operation: Laser cutting works by directing a concentrated beam of coherent light energy (laser) onto the surface of the workpiece, which melts, burns, or vaporizes the material along the desired cutting path. The laser beam is generated by a laser resonator and focused through a series of mirrors or lenses onto the workpiece, creating a narrow kerf width and achieving precise cuts.
- Materials: Laser cutting is suitable for cutting a wide range of materials, including metals (such as steel, stainless steel, aluminum, brass, and copper), plastics, composites, wood, and textiles. It can effectively cut materials of varying thicknesses, from thin foils and sheets to thicker plates and profiles, making it a versatile choice for many applications.
- Advantages:
- Precision: Laser cutting offers high precision and accuracy, with the ability to achieve tight tolerances (typically ±0.1 mm) and intricate geometries with sharp corners and fine details.
- Speed: Laser cutting is a fast and efficient process, with cutting speeds that exceed those of traditional mechanical cutting methods such as sawing or shearing.
- Versatility: Laser cutting is versatile and adaptable to a wide variety of materials and thicknesses, making it suitable for a broad range of applications across different industries.
- Minimal Material Waste: Laser cutting produces minimal material waste due to its narrow kerf width and the ability to nest parts closely together on the material sheet, optimizing material utilization and reducing costs.
- Non-Contact Cutting: Laser cutting is a non-contact cutting method, which means there is no physical contact between the cutting tool and the workpiece. This reduces the risk of tool wear, damage to delicate materials, and contamination of the workpiece surface.
- Automation and Integration: Laser cutting can be easily automated and integrated into computer-controlled manufacturing systems, allowing for efficient production runs, batch processing, and rapid prototyping.
- Applications:
- Industrial Manufacturing: Laser cutting is widely used in industrial manufacturing for cutting sheet metal, tubes, and profiles to create components and assemblies for various industries, including automotive, aerospace, electronics, and machinery.
- Signage and Display: Laser cutting is utilized in the signage and display industry for cutting letters, logos, and decorative elements from materials such as acrylic, aluminum, and wood for indoor and outdoor signage, exhibits, and promotional displays.
- Architectural and Decorative: Laser cutting is employed in architectural and decorative applications for cutting intricate patterns, designs, and motifs from materials such as stainless steel, aluminum, and glass for building facades, interior decor, and ornamental features.
- Jewelry and Fashion: Laser cutting is popular in the jewelry and fashion industries for cutting intricate designs, patterns, and textures from precious metals, gemstones, leather, and fabric for jewelry, accessories, and apparel.
- Medical and Dental: Laser cutting is used in the medical and dental fields for cutting surgical instruments, implants, orthodontic appliances, and prosthetics from biocompatible materials such as titanium, stainless steel, and polymers.
- Limitations:
- Material Thickness: Laser cutting is most effective for cutting thin to medium thickness materials (up to several centimeters), and may be less efficient or cost-effective for cutting thicker materials.
- Material Compatibility: Some materials are not suitable for laser cutting due to their composition, such as materials that are highly reflective, transparent, or prone to burning or melting.
- Initial Investment: The initial investment cost for laser cutting equipment may be higher compared to other cutting methods, although operational costs can be lower due to reduced tooling wear and maintenance requirements.
In summary, laser cutting is a versatile and precise metal fabrication process that offers high accuracy, speed, and versatility for cutting a wide range of materials and geometries. Its applications span various industries, from industrial manufacturing and signage to architectural design and jewelry making, making it a valuable technology in modern production and design processes.
Plasma Cutting:
Plasma cutting is a metal fabrication process that uses a high-velocity jet of ionized gas (plasma) to cut through electrically conductive materials such as steel, stainless steel, aluminum, copper, and other metals. It offers several advantages, including high cutting speeds, versatility, and the ability to cut thick materials with minimal distortion.
- Principle of Operation: Plasma cutting works by passing an electrical current through a gas (typically compressed air, nitrogen, or oxygen) to create a plasma arc. The plasma arc is directed through a constricted nozzle at the workpiece, where it heats the material to its melting point and blows away the molten metal, creating a kerf and achieving a clean cut.
- Materials: Plasma cutting is suitable for cutting electrically conductive materials, including ferrous and non-ferrous metals, with thicknesses ranging from thin sheets to thick plates. It is commonly used in industries such as metal fabrication, construction, automotive, shipbuilding, and aerospace.
- Advantages:
- High Cutting Speeds: Plasma cutting offers high cutting speeds, making it a fast and efficient process for cutting thick materials and large volumes of parts.
- Versatility: Plasma cutting is versatile and adaptable to a wide range of materials, thicknesses, and geometries, making it suitable for various applications across different industries.
- Thick Material Cutting: Plasma cutting can cut through thick materials (up to several inches) with ease, making it ideal for heavy-duty applications such as structural steel fabrication, shipbuilding, and heavy machinery manufacturing.
- Minimal Distortion: Plasma cutting produces minimal heat-affected zones (HAZ) and distortion in the workpiece, resulting in clean, straight cuts with minimal thermal deformation.
- Portability: Plasma cutting systems are often portable and lightweight, allowing for on-site cutting and fabrication in remote locations or construction sites.
- Applications:
- Metal Fabrication: Plasma cutting is widely used in metal fabrication shops for cutting sheet metal, plates, pipes, and structural components for various industries, including construction, manufacturing, and infrastructure.
- Automotive and Transportation: Plasma cutting is employed in the automotive and transportation industries for cutting chassis components, body panels, frames, and exhaust systems from steel, aluminum, and other metals.
- Shipbuilding and Marine: Plasma cutting is utilized in shipbuilding and marine construction for cutting hulls, decks, bulkheads, and pipe fittings from steel and aluminum alloys, as well as for repair and maintenance operations.
- Construction and Infrastructure: Plasma cutting is used in construction and infrastructure projects for cutting structural steel beams, columns, plates, and pipe sections for buildings, bridges, highways, and pipelines.
- Demolition and Recycling: Plasma cutting is applied in demolition and recycling operations for cutting scrap metal, dismantling structures, and processing recyclable materials for reuse.
- Limitations:
- Material Thickness: While plasma cutting is effective for cutting thick materials, it may not be as precise or economical for cutting thin materials (
- Edge Quality: Plasma cutting may produce rougher edges and a wider kerf compared to laser cutting, requiring additional finishing operations if a smoother surface finish is desired.
- Environmental Considerations: Plasma cutting generates noise, fumes, and ultraviolet (UV) radiation during the cutting process, requiring proper ventilation, safety measures, and personal protective equipment (PPE) to minimize exposure and comply with regulations.
In summary, plasma cutting is a versatile and efficient metal fabrication process that offers high cutting speeds, versatility, and the ability to cut thick materials with minimal distortion. Its applications span various industries, including metal fabrication, automotive, shipbuilding, construction, and recycling, making it a valuable technology in modern manufacturing and construction processes.
Sheet Metal Forming:
Sheet metal forming is a metalworking process used to shape flat sheets of metal into desired geometries, contours, and configurations. It encompasses a variety of techniques and operations, each tailored to specific requirements, materials, and end-use applications.
- Principle of Operation: Sheet metal forming involves the application of mechanical force, heat, or pressure to deform metal sheets, causing them to bend, stretch, or compress into the desired shape. The process may be performed at room temperature (cold forming) or elevated temperatures (hot forming), depending on the material properties and forming requirements.
- Types of Forming Operations:
- Bending: Bending is the most common sheet metal forming operation, where metal sheets are bent along a straight axis using a press brake or bending machine. Different bending techniques include air bending, bottom bending, coining, and roll bending, each producing specific bend angles, radii, and geometries.
- Stretching: Stretch forming stretches metal sheets over a die to form three-dimensional shapes or contours, typically used for automotive body panels, aircraft fuselages, and architectural components.
- Deep Drawing: Deep drawing pulls metal sheets into a die cavity to create hollow or cup-shaped parts, such as kitchen sinks, automotive fuel tanks, and beverage cans.
- Spinning: Spinning rotates metal sheets or blanks against a rotating mandrel to form cylindrical or conical shapes, commonly used for producing metal vessels, lampshades, and architectural features.
- Embossing and Coining: Embossing raises or depresses metal surfaces to create decorative patterns, logos, or textures, enhancing aesthetic appeal or functional properties. Coining compresses metal sheets to imprint designs or lettering for identification or branding purposes.
- Materials: Sheet metal forming can be performed on a wide range of materials, including steel, aluminum, stainless steel, copper, brass, titanium, and alloys. Material selection depends on factors such as mechanical properties, formability, corrosion resistance, and cost considerations.
- Tooling and Equipment:
- Press Brakes: Press brakes are used for bending metal sheets into various angles and shapes. They consist of a punch (upper die) and a die (lower die) mounted on a hydraulic or mechanical press, capable of exerting high forces to deform the metal.
- Stamping Presses: Stamping presses are used for punching, blanking, and forming metal sheets into specific shapes and contours. They utilize dies, punches, and tooling assemblies to apply force and shape the metal through successive operations.
- Roll Forming Machines: Roll forming machines gradually shape metal sheets or strips by passing them through a series of rollers, producing continuous profiles, curves, or complex shapes.
- Hydroforming Equipment: Hydroforming uses hydraulic pressure to shape metal sheets or tubes into complex geometries using a fluid-filled chamber or bladder. It is commonly used for automotive chassis components, bicycle frames, and aerospace structures.
- Design Considerations:
- Bend Allowance: The bend allowance accounts for material elongation and compression during bending operations, ensuring accurate dimensions and tolerances in the finished part.
- Forming Limits: The forming limits of the material dictate its maximum stretchability and deformation capabilities without fracturing or wrinkling, influencing the design of complex shapes and contours.
- Springback: Springback refers to the elastic recovery of the material after forming, which can cause dimensional inaccuracies in the finished part and require compensation in tooling design and process parameters.
- Draft Angles: Draft angles are incorporated into part designs to facilitate material flow and release during forming operations, minimizing friction, wrinkling, and surface defects.
- Applications:
- Automotive: Sheet metal forming is widely used in the automotive industry for producing body panels, chassis components, structural reinforcements, and interior trim from steel, aluminum, and advanced high-strength alloys.
- Aerospace: Sheet metal forming is employed in the aerospace industry for manufacturing aircraft fuselages, wings, empennages, and engine components from aluminum, titanium, and composite materials.
- Electronics: Sheet metal forming is utilized in the electronics industry for fabricating enclosures, cabinets, heat sinks, and chassis for electronic devices, telecommunications equipment, and computer hardware.
- Appliances: Sheet metal forming is applied in the appliance industry for producing kitchen appliances, HVAC systems, washing machines, dryers, and refrigerators from stainless steel, aluminum, and coated metals.
- Construction: Sheet metal forming is used in the construction industry for manufacturing architectural cladding, roofing panels, curtain walls, and structural components from aluminum, steel, and composite materials.
In summary, sheet metal forming is a versatile and essential metalworking process that encompasses various techniques and operations for shaping metal sheets into desired forms and configurations. Its applications span diverse industries, from automotive and aerospace to electronics, appliances, and construction, contributing to the production of a wide range of components and assemblies used in modern infrastructure and technology.
Stamping and Punching:
Stamping and punching are metal fabrication processes used to create holes, cutouts, and features in sheet metal parts through the application of mechanical force using punches and dies. These processes are essential in manufacturing industries for producing components with precise dimensions, shapes, and configurations.
- Principle of Operation:
- Stamping: Stamping involves pressing a punch (male) and a die (female) together against a metal sheet to deform the material and create a desired shape or feature. The punch applies force to the workpiece, causing it to undergo plastic deformation and take the shape of the die cavity.
- Punching: Punching uses a single punch tool to penetrate the metal sheet and create a hole, slot, or cutout. The punch exerts sufficient force to shear the material and form the desired feature, typically in one swift motion.
- Materials:
- Stamping and punching can be performed on a wide range of sheet metal materials, including steel, aluminum, stainless steel, copper, brass, and various alloys. Material selection depends on factors such as mechanical properties, corrosion resistance, and end-use requirements.
- Types of Operations:
- Blanking: Blanking is the process of cutting flat shapes or profiles from a metal sheet, leaving the desired part shape as the finished product. It involves shearing the material along a straight line using a punch and die set.
- Piercing: Piercing creates holes, slots, or openings in the metal sheet using a punch and die set. The punch penetrates the workpiece, shearing the material and forming the desired feature, such as mounting holes or slots for fasteners.
- Notching: Notching removes material from the edge or corner of a metal sheet to create a tab, notch, or profile. It is commonly used for creating interlocking features or facilitating assembly of components.
- Coining: Coining compresses the metal sheet between the punch and die to imprint designs, logos, or lettering onto the surface. It is often used for branding, identification, or decorative purposes.
- Tooling and Equipment:
- Punch Presses: Punch presses are specialized machines equipped with a ram (punch) and a bolster (die) for performing stamping and punching operations. They exert high forces and precise control to deform metal sheets and create complex shapes.
- Tool and Die Sets: Tool and die sets consist of hardened steel punches and dies, custom-designed to match the desired part geometry and specifications. They are precision-engineered to withstand the forces involved in stamping and punching operations.
- Applications:
- Automotive Industry: Stamping and punching are extensively used in the automotive industry for producing body panels, chassis components, brackets, and reinforcements. Punching operations create holes for mounting hardware, fasteners, and electrical connections.
- Electronics Manufacturing: Stamping and punching are employed in the electronics industry for fabricating enclosures, brackets, heat sinks, and connectors. Precision punching operations create openings for switches, displays, ports, and ventilation.
- Appliance Production: Stamping and punching play a crucial role in appliance manufacturing for producing housing, panels, doors, and internal components. Notching operations create tabs and profiles for assembly, while piercing operations create holes for handles, hinges, and controls.
- Aerospace Sector: Stamping and punching are used in the aerospace industry for manufacturing structural components, brackets, and hardware. Precision punching operations create holes for fasteners, wiring, and instrumentation in aircraft assemblies and interior fittings.
- Quality Control:
- Dimensional Accuracy: Quality control measures ensure that stamped and punched parts meet specified dimensional tolerances and fitment requirements. Inspection tools such as calipers, micrometers, and CMMs (Coordinate Measuring Machines) are used to verify part dimensions.
- Surface Finish: Surface inspection ensures that stamped and punched parts have smooth edges, uniform finishes, and no burrs or defects. Visual inspection, deburring processes, and surface treatment techniques are employed to achieve desired surface quality.
- Material Integrity: Material testing and analysis techniques are used to ensure that stamped and punched parts exhibit the required mechanical properties, such as tensile strength, ductility, and hardness. Non-destructive testing methods may be employed to detect defects or anomalies in the material structure.
In summary, stamping and punching are fundamental metal fabrication processes used to create holes, cutouts, and features in sheet metal parts for various industries. These processes offer high precision, repeatability, and efficiency, contributing to the production of complex components and assemblies with tight tolerances and functional requirements.
Welding:
Welding is a metal fabrication process used to join two or more pieces of metal together by melting and fusing them at the joint. It is a fundamental technique in manufacturing and construction industries for creating strong and durable connections between metal components.
- Principle of Operation:
- Welding involves applying heat to the metal pieces at the joint until they reach their melting point, forming a molten pool of metal. A filler material may be added to the joint to enhance the strength and integrity of the weld.
- As the molten metal cools and solidifies, it forms a strong bond between the welded components, creating a continuous and permanent joint.
- Types of Welding Processes:
- Arc Welding: Arc welding uses an electric arc between an electrode and the workpiece to generate heat and melt the metal. Common types of arc welding include:
- Shielded Metal Arc Welding (SMAW)
- Gas Metal Arc Welding (GMAW)
- Flux-Cored Arc Welding (FCAW)
- Gas Tungsten Arc Welding (GTAW)
- Resistance Welding: Resistance welding applies pressure and electrical resistance to the metal pieces, causing them to heat up and fuse together. Examples of resistance welding processes include spot welding, seam welding, and projection welding.
- Gas Welding: Gas welding uses a flame produced by burning a fuel gas (such as acetylene) with oxygen to generate heat for melting the metal. It is commonly used for welding non-ferrous metals such as aluminum and copper.
- Laser Welding: Laser welding uses a highly focused laser beam to heat and melt the metal at the joint. It offers high precision, minimal distortion, and fast welding speeds, making it suitable for precision welding applications.
- Electron Beam Welding: Electron beam welding uses a high-energy electron beam to heat and weld the metal components in a vacuum environment. It is capable of producing deep penetration welds with minimal heat-affected zones.
- Materials:
- Welding can be performed on a wide range of metals and alloys, including steel, stainless steel, aluminum, copper, brass, titanium, and their alloys. Material selection depends on factors such as mechanical properties, corrosion resistance, and end-use requirements.
- Joint Design and Preparation:
- Proper joint design and preparation are essential for producing high-quality welds. Common types of weld joints include butt joints, lap joints, fillet joints, and T-joints, each requiring specific preparation and welding techniques.
- Joint preparation involves cleaning the metal surfaces, removing any contaminants or oxides, and ensuring proper fit-up and alignment between the welded components.
- Welding Safety:
- Welding poses various hazards to the operator and surrounding environment, including arc radiation, heat, fumes, and metal spatter. Proper safety measures, including personal protective equipment (PPE), ventilation systems, and welding screens, are essential to protect against these hazards.
- Welding operators should be trained in safe welding practices and techniques to minimize the risk of accidents, injuries, and occupational hazards.
- Applications:
- Manufacturing: Welding is used in manufacturing industries for fabricating metal structures, assemblies, and components, including automotive parts, machinery, equipment, and appliances.
- Construction: Welding plays a crucial role in construction projects for joining structural steel beams, columns, and plates in buildings, bridges, infrastructure, and offshore platforms.
- Aerospace and Defense: Welding is employed in the aerospace and defense sectors for manufacturing aircraft frames, fuselages, engine components, and military vehicles.
- Shipbuilding: Welding is extensively used in shipbuilding and marine construction for welding hulls, decks, bulkheads, and piping systems in ships, boats, and offshore structures.
- Pipeline and Oil/Gas Industry: Welding is essential for joining pipelines, pressure vessels, storage tanks, and process equipment in the oil, gas, and petrochemical industries.
In summary, welding is a versatile and widely used metal fabrication process for joining metal components and structures in various industries. It offers flexibility, strength, and efficiency in creating durable connections, making it indispensable in modern manufacturing, construction, and infrastructure projects.
CNC Machining:
CNC (Computer Numerical Control) machining is a manufacturing process that uses computerized controls and precise cutting tools to remove material from a workpiece to create a desired shape or part. It is widely used in metal fabrication for producing components with high precision, accuracy, and repeatability.
- Principle of Operation:
- CNC machining operates based on digital instructions (G-code) programmed into a computerized control system. The CNC machine interprets these instructions to move cutting tools along multiple axes (typically three or more) to remove material from the workpiece.
- Cutting tools such as drills, end mills, and lathes are mounted on the CNC machine’s spindle and controlled by servo motors, allowing for precise positioning and movement in three-dimensional space.
- CNC machining can perform various operations, including milling, turning, drilling, threading, and grinding, to produce complex geometries and features on metal workpieces.
- Materials:
- CNC machining can be performed on a wide range of metals and alloys, including steel, stainless steel, aluminum, brass, copper, titanium, and exotic alloys. Material selection depends on factors such as mechanical properties, hardness, and end-use requirements.
- Types of CNC Machines:
- CNC Milling Machines: CNC milling machines use rotating cutting tools to remove material from a workpiece to create flat or contoured surfaces. They are versatile and capable of producing complex shapes and features with high precision.
- CNC Turning Machines: CNC turning machines rotate the workpiece while cutting tools remove material to create cylindrical or conical shapes. They are used for producing shafts, pins, bushings, and other rotationally symmetric components.
- CNC Machining Centers: CNC machining centers combine milling, drilling, and tapping operations into a single machine, allowing for multi-axis machining and simultaneous machining of multiple surfaces.
- CNC Lathes: CNC lathes are specialized turning machines equipped with computer-controlled tooling and spindle movements for producing precision-turned parts with tight tolerances and surface finishes.
- Advantages:
- Precision and Accuracy: CNC machining offers high precision and accuracy, with the ability to achieve tight tolerances (typically within ±0.001 inches or 0.025 mm) and fine surface finishes.
- Versatility: CNC machining is versatile and adaptable to a wide range of geometries, materials, and part sizes, making it suitable for prototyping, custom fabrication, and high-volume production.
- Automation: CNC machining can be fully automated or semi-automated, reducing the need for manual intervention and increasing productivity, repeatability, and throughput.
- Flexibility: CNC machining allows for rapid setup and changeover between different part designs and production runs, enabling manufacturers to respond quickly to changing market demands and customer requirements.
- Complex Geometries: CNC machining can produce complex shapes, contours, and features that may be difficult or impossible to achieve with conventional machining methods.
- Applications:
- Aerospace and Defense: CNC machining is widely used in the aerospace and defense industries for producing aircraft components, missile parts, engine components, and precision instruments with tight tolerances and stringent quality requirements.
- Automotive: CNC machining is employed in the automotive industry for manufacturing engine blocks, cylinder heads, transmission components, suspension parts, and brake systems with high precision and consistency.
- Medical Devices: CNC machining is used in the medical device industry for fabricating surgical instruments, implants, orthopedic devices, and prosthetics from biocompatible materials with precise dimensions and surface finishes.
- Electronics and Consumer Goods: CNC machining is utilized in the electronics and consumer goods industries for producing enclosures, housings, connectors, and components with intricate designs and functional features.
- Tool and Die Making: CNC machining is essential for manufacturing molds, dies, jigs, and fixtures used in injection molding, casting, stamping, and assembly operations across various industries.
In summary, CNC machining is a versatile and precise metal fabrication process that offers high precision, accuracy, and repeatability in producing complex components and parts for various industries. Its ability to automate production, achieve tight tolerances, and work with a wide range of materials makes it a fundamental technology in modern manufacturing and engineering processes.
Waterjet Cutting:
Waterjet cutting is a versatile and precise metal fabrication process that utilizes a high-pressure jet of water mixed with an abrasive substance to cut through various materials. It offers several advantages, including high accuracy, minimal heat-affected zones, and the ability to cut a wide range of materials and thicknesses.
- Principle of Operation:
- Waterjet cutting works by pressurizing water to extremely high levels (typically between 40,000 to 90,000 psi) and forcing it through a small nozzle at high velocity. In abrasive waterjet cutting, fine abrasive particles, such as garnet, are added to the water stream to enhance cutting performance.
- The high-pressure water jet erodes the material at the cut line, gradually forming a narrow kerf width and achieving precise cuts. The abrasive particles in the water jet help to accelerate the cutting process and improve cutting efficiency, especially for hard and dense materials.
- Materials:
- Waterjet cutting can be used to cut a wide range of materials, including metals (such as steel, stainless steel, aluminum, brass, copper), ceramics, glass, composites, plastics, stone, and even some hard materials like titanium and hardened tool steels. It is suitable for cutting materials of varying thicknesses, from thin foils and sheets to thick plates and blocks.
- Advantages:
- Precision: Waterjet cutting offers high precision and accuracy, with the ability to achieve tight tolerances (typically ±0.1 mm) and intricate geometries with sharp corners and fine details.
- Minimal Heat-Affected Zones: Waterjet cutting produces minimal heat-affected zones (HAZ) in the material, reducing the risk of thermal distortion, warping, or metallurgical changes, especially in heat-sensitive materials.
- Versatility: Waterjet cutting is versatile and adaptable to a wide variety of materials and thicknesses, making it suitable for a broad range of applications across different industries.
- No Tool Wear: Waterjet cutting is a non-contact cutting method, which means there is no physical contact between the cutting tool and the workpiece. This eliminates tool wear and reduces the need for frequent tool changes or sharpening.
- Environmentally Friendly: Waterjet cutting is considered an environmentally friendly cutting method, as it does not generate hazardous fumes, dust, or by-products during the cutting process. It also uses water as the primary cutting medium, which can be recycled and reused in closed-loop systems.
- Applications:
- Metal Fabrication: Waterjet cutting is widely used in metal fabrication shops for cutting sheet metal, plates, tubes, and profiles to create components and assemblies for various industries, including automotive, aerospace, marine, and architectural.
- Architectural and Decorative: Waterjet cutting is employed in architectural and decorative applications for cutting intricate patterns, designs, and motifs from metals, glass, stone, and tile for building facades, interior decor, and ornamental features.
- Aerospace and Defense: Waterjet cutting is utilized in the aerospace and defense industries for cutting aircraft components, engine parts, armor plating, and composite materials with high precision and consistency.
- Automotive: Waterjet cutting is used in the automotive industry for cutting chassis components, body panels, gaskets, and interior trim from metals and non-metallic materials with tight tolerances and complex shapes.
- Industrial Manufacturing: Waterjet cutting is applied in various industrial manufacturing processes for cutting parts, components, and assemblies from a wide range of materials, including machine components, tooling, and prototypes.
- Limitations:
- Speed: While waterjet cutting offers high precision and versatility, it may not be as fast as other cutting methods such as laser cutting or plasma cutting, especially for thicker materials or large-volume production runs.
- Operating Costs: The operating costs of waterjet cutting systems, including equipment maintenance, consumables (such as abrasive materials), and energy consumption, may be higher compared to some other cutting methods, although the benefits of precision and versatility often outweigh the costs.
In summary, waterjet cutting is a versatile and precise metal fabrication process that offers high accuracy, minimal heat-affected zones, and the ability to cut a wide range of materials and thicknesses. Its applications span various industries, from metal fabrication and aerospace to architecture, automotive, and industrial manufacturing, making it a valuable technology in modern production and design processes.
Grinding:
Grinding is a metal fabrication process used to remove material from a workpiece’s surface through abrasive cutting, generating a smooth and precise finish. It is commonly used to achieve tight tolerances, improve surface quality, and create specific geometries on metallic components.
- Principle of Operation:
- Grinding involves the use of abrasive grains bonded together in a grinding wheel or abrasive belt to remove material from the workpiece’s surface. The abrasive grains act as cutting tools, continuously removing small amounts of material through high-speed rotation or linear movement.
- The grinding wheel or abrasive belt is pressed against the workpiece with controlled force, resulting in material removal and the formation of a desired surface finish. Various factors such as wheel speed, feed rate, and depth of cut influence the grinding process’s efficiency and effectiveness.
- Types of Grinding Processes:
- Surface Grinding: Surface grinding is used to produce a smooth and flat surface finish on metallic workpieces. A horizontal spindle grinder or a vertical spindle grinder with a reciprocating table is used to traverse the grinding wheel across the workpiece’s surface.
- Cylindrical Grinding: Cylindrical grinding is employed to produce cylindrical or round components with precise dimensions and surface finishes. The workpiece rotates on a central axis while the grinding wheel traverses along its length to remove material and create the desired shape.
- Centerless Grinding: Centerless grinding is a machining process where the workpiece is supported between two wheels (a grinding wheel and a regulating wheel) and rotated at high speed while the grinding wheel removes material from the workpiece’s outer diameter.
- Internal Grinding: Internal grinding is used to produce precise bores, holes, and internal features inside cylindrical workpieces. The grinding wheel is mounted on a spindle and traversed into the workpiece’s interior to remove material and achieve the desired dimensions and surface finish.
- Tool and Cutter Grinding: Tool and cutter grinding is employed to sharpen cutting tools, such as drills, end mills, reamers, and broaches, to maintain their cutting performance and extend tool life.
- Materials:
- Grinding can be performed on a wide range of metallic materials, including steel, stainless steel, aluminum, titanium, brass, copper, and various alloys. Material selection depends on factors such as hardness, machinability, and end-use requirements.
- Advantages:
- Precision and Accuracy: Grinding offers high precision and accuracy, with the ability to achieve tight tolerances (typically within microns) and fine surface finishes, making it suitable for producing components with demanding dimensional and geometric requirements.
- Surface Finish: Grinding produces smooth and uniform surface finishes, free of scratches, burrs, and irregularities, enhancing the workpiece’s appearance, functionality, and performance.
- Material Removal Rate: Grinding can remove material quickly and efficiently, allowing for rapid stock removal and the production of parts with minimal machining time.
- Tooling Flexibility: Grinding wheels and abrasive belts are available in various shapes, sizes, and abrasive compositions, offering flexibility in tool selection and customization to meet specific machining requirements.
- Versatility: Grinding can be applied to a wide range of workpiece geometries, sizes, and configurations, making it suitable for diverse applications across different industries and manufacturing processes.
- Applications:
- Precision Engineering: Grinding is widely used in precision engineering industries for producing high-precision components, such as bearings, shafts, gears, valves, and tooling, with tight dimensional tolerances and surface finishes.
- Automotive Manufacturing: Grinding is employed in automotive manufacturing for producing engine components, transmission parts, brake rotors, and camshafts with precise dimensions and surface qualities.
- Aerospace Industry: Grinding plays a critical role in the aerospace industry for manufacturing aircraft components, turbine blades, landing gear, and aerospace structures with stringent quality requirements and performance standards.
- Mold and Die Making: Grinding is utilized in mold and die making for producing injection molds, die casting dies, and stamping dies with complex geometries and fine surface finishes to ensure accurate and repeatable molding and forming processes.
- Medical Device Production: Grinding is used in the medical device industry for manufacturing surgical instruments, implants, prosthetics, and medical devices with precise features and biocompatible surface finishes.
In summary, grinding is a versatile and precise metal fabrication process used to achieve tight tolerances, improve surface finishes, and create specific geometries on metallic components. Its applications span various industries, from precision engineering and automotive manufacturing to aerospace, mold making, and medical device production, making it a fundamental technology in modern manufacturing and engineering processes.
Sheet Metal Forming:
Sheet metal forming is a metal fabrication process that transforms flat metal sheets into desired shapes and configurations through plastic deformation. It encompasses various techniques, including bending, stretching, deep drawing, and forming, to produce a wide range of components and products used in diverse industries.
- Principle of Operation:
- Sheet metal forming utilizes mechanical forces to shape flat metal sheets into three-dimensional parts. The process involves applying controlled pressure and stress to the metal sheet, causing it to undergo plastic deformation and take on the shape of a die or mold.
- Depending on the specific forming technique employed, the metal sheet may be stretched, bent, drawn, or compressed to achieve the desired geometry and dimensional accuracy.
- Types of Sheet Metal Forming Processes:
- Bending: Bending involves deforming a metal sheet along a straight axis to create angular or curved shapes. It is commonly performed using press brakes, roll forming machines, or specialized bending tools to achieve precise bend angles and radii.
- Stretching: Stretch forming stretches a metal sheet over a die or form tool to create contoured or irregular shapes. The sheet is clamped around its edges, and a stretching force is applied to elongate and shape the material over the form.
- Deep Drawing: Deep drawing is used to form cylindrical or box-shaped components from flat metal blanks. The metal blank is placed over a die cavity and drawn into the cavity using a punch, creating a seamless and uniform part with consistent wall thickness.
- Stamping: Stamping involves pressing a punch and die together to cut, pierce, or form metal sheets into specific shapes and configurations. It is used for producing complex geometries, holes, slots, and features in sheet metal parts.
- Hydroforming: Hydroforming uses hydraulic fluid pressure to shape metal sheets into intricate forms and contours. The metal sheet is clamped over a die cavity and pressurized with hydraulic fluid to force it into the desired shape.
- Spinning: Spinning involves rotating a metal disc or blank against a rotating mandrel to form symmetrical shapes, such as cones, cylinders, and domes. The metal blank is gradually shaped and stretched using specialized spinning tools and techniques.
- Materials:
- Sheet metal forming can be performed on a wide range of metallic materials, including steel, stainless steel, aluminum, copper, brass, titanium, and their alloys. Material selection depends on factors such as mechanical properties, formability, and end-use requirements.
- Advantages:
- Design Flexibility: Sheet metal forming offers design flexibility, allowing for the creation of complex shapes, contours, and configurations that may be difficult or costly to achieve using other manufacturing methods.
- High Production Efficiency: Sheet metal forming processes can be highly automated and adapted for high-volume production, enabling manufacturers to produce large quantities of parts with consistent quality and dimensional accuracy.
- Material Utilization: Sheet metal forming minimizes material waste by optimizing the layout and nesting of parts on metal sheets, reducing scrap and maximizing material utilization.
- Cost-Effectiveness: Sheet metal forming is a cost-effective manufacturing process, offering low tooling costs, short setup times, and efficient production rates compared to other fabrication methods.
- Strength and Structural Integrity: Sheet metal formed components exhibit high strength, stiffness, and structural integrity, making them suitable for structural applications, enclosures, housings, and assemblies.
- Applications:
- Automotive Industry: Sheet metal forming is extensively used in the automotive industry for producing body panels, chassis components, brackets, frames, and structural reinforcements.
- Aerospace and Defense: Sheet metal forming plays a critical role in the aerospace and defense sectors for manufacturing aircraft structures, fuselage panels, wing skins, engine components, and missile casings.
- Appliance Manufacturing: Sheet metal forming is employed in appliance manufacturing for fabricating enclosures, doors, panels, and internal components of household appliances such as refrigerators, ovens, washers, and dryers.
- Electronics and Electrical Equipment: Sheet metal forming is utilized in the electronics industry for producing enclosures, cabinets, racks, chassis, and mounting hardware for electronic devices, telecommunications equipment, and control panels.
- Construction and Architecture: Sheet metal forming is applied in the construction and architectural industries for fabricating architectural elements, façade panels, roofing systems, cladding, and decorative features in buildings and structures.
In summary, sheet metal forming is a versatile and widely used metal fabrication process that transforms flat metal sheets into three-dimensional parts with complex shapes and configurations. Its applications span various industries, including automotive, aerospace, appliance manufacturing, electronics, construction, and architecture, making it an indispensable technology in modern manufacturing and engineering processes.
Punching:
Punching is a metal fabrication process used to create holes, notches, and other features in sheet metal and other thin materials. It involves using a punch and die set to apply force and shear the material, resulting in the desired shape or cutout.
- Principle of Operation:
- Punching operates on the principle of shearing, where a punch tool exerts force on the workpiece against a die, causing the material to fracture and form the desired hole or feature.
- The punch tool, typically mounted on a press machine, applies a downward force to penetrate the workpiece, while the die supports the material and provides clearance for the punch to pass through.
- Types of Punching Operations:
- Piercing: Piercing involves creating holes or openings in the workpiece by pushing the punch through the material. It is commonly used for producing holes of various shapes and sizes in sheet metal panels, plates, and components.
- Blanking: Blanking is similar to piercing but involves removing a portion of the material to create a flat, defined shape. The punched-out piece, known as a blank, is separated from the surrounding material, leaving a hole or cutout in the workpiece.
- Notching: Notching is used to create irregularly shaped cutouts or notches in the edges or corners of the workpiece. It is often employed for forming tabs, slots, and other features in sheet metal parts for assembly or joining purposes.
- Punching and Forming: Punching can be combined with forming operations to create complex shapes and features in sheet metal components. The punch may be designed with additional features, such as embossing, coining, or extruding, to shape the material during the punching process.
- Materials:
- Punching can be performed on various materials, including steel, stainless steel, aluminum, copper, brass, and plastics. Material thicknesses typically range from thin gauge sheets (e.g., 0.5 mm) to thicker plates (e.g., 6 mm), depending on the punching equipment and capabilities.
- Advantages:
- High Speed: Punching is a fast and efficient metal fabrication process, capable of producing multiple holes or features in a single operation, thereby reducing cycle times and increasing productivity.
- Precision and Accuracy: Punching offers high precision and dimensional accuracy, with the ability to create holes and features with tight tolerances and consistent quality across large production batches.
- Versatility: Punching can be adapted to create a wide range of hole sizes, shapes, and configurations, making it suitable for various applications in industries such as automotive, electronics, construction, and manufacturing.
- Cost-Effectiveness: Punching is a cost-effective method for creating holes and features in sheet metal and thin materials, offering low tooling costs, short setup times, and minimal material waste compared to alternative processes such as drilling or milling.
- Automation: Punching operations can be fully automated using CNC (Computer Numerical Control) punching machines, allowing for high-speed, high-volume production with minimal operator intervention.
- Applications:
- Sheet Metal Fabrication: Punching is widely used in sheet metal fabrication shops for creating holes, cutouts, and features in sheet metal components used in enclosures, cabinets, panels, brackets, and assemblies.
- Electrical and Electronics: Punching is employed in the electrical and electronics industries for producing PCB (Printed Circuit Board) enclosures, control panels, junction boxes, and mounting hardware with precision-cut holes for connectors, switches, and cables.
- Automotive Manufacturing: Punching is utilized in automotive manufacturing for creating holes, slots, and features in body panels, chassis components, engine covers, and interior trim parts with high precision and repeatability.
- Construction and Architecture: Punching is applied in the construction and architectural industries for fabricating metal panels, façades, cladding systems, and decorative elements with standardized hole patterns and profiles for ventilation, drainage, and aesthetics.
- Furniture and Appliances: Punching is used in the furniture and appliance industries for creating holes, slots, and cutouts in metal frames, brackets, shelves, and panels for assembly and mounting of hardware, hinges, and accessories.
In summary, punching is a versatile and efficient metal fabrication process used to create holes, cutouts, and features in sheet metal and thin materials. Its applications span various industries, including sheet metal fabrication, electrical and electronics, automotive manufacturing, construction, furniture, and appliances, making it a fundamental technology in modern manufacturing and engineering processes.
Welding:
Welding is a metal fabrication process used to join two or more metal parts together by melting and fusing them into a single piece. It plays a crucial role in manufacturing, construction, and repair applications across various industries.
- Principle of Operation:
- Welding works on the principle of creating a strong and permanent bond between metal parts by heating them to their melting point and allowing them to fuse together.
- A heat source, such as an electric arc, gas flame, or laser beam, is used to generate the necessary heat energy to melt the base metals and filler material (if used) at the joint interface.
- The molten metal forms a pool or weld puddle, which solidifies upon cooling, creating a metallurgical bond between the adjacent metal surfaces.
- Types of Welding Processes:
- Arc Welding: Arc welding uses an electric arc between an electrode and the workpiece to generate heat and create the weld. Common arc welding methods include Shielded Metal Arc Welding (SMAW), Gas Metal Arc Welding (GMAW), and Gas Tungsten Arc Welding (GTAW).
- Gas Welding: Gas welding, also known as oxy-fuel welding, utilizes a flame produced by the combustion of a fuel gas (e.g., acetylene) and oxygen to heat and melt the base metals. It is commonly used for welding thin metals and in repair applications.
- Resistance Welding: Resistance welding applies pressure and electrical current to the metal parts to be joined, causing resistance heating at the interface and forming the weld. Spot welding and seam welding are common forms of resistance welding.
- Laser Welding: Laser welding employs a highly concentrated laser beam to melt and fuse the metal parts together. It offers high precision and control, making it suitable for welding small and intricate components.
- Electron Beam Welding: Electron beam welding uses a focused beam of high-velocity electrons to heat and weld the metal parts in a vacuum chamber. It is used for welding thick materials and in aerospace and automotive applications.
- Materials:
- Welding can be performed on a wide range of metallic materials, including steel, stainless steel, aluminum, copper, brass, titanium, nickel alloys, and their combinations. The choice of welding process and consumables depends on the specific material properties and application requirements.
- Advantages:
- Strength and Durability: Welding creates strong and durable joints, capable of withstanding high loads, stresses, and environmental conditions, making it suitable for structural applications in construction, automotive, and aerospace industries.
- Versatility: Welding can join a variety of metal types, shapes, and thicknesses, allowing for the fabrication of complex assemblies and structures with customized designs and configurations.
- Efficiency: Welding offers high production efficiency, with the ability to join multiple parts in a single operation and minimal material waste compared to mechanical joining methods such as bolting or riveting.
- Cost-Effectiveness: Welding is a cost-effective joining method for large-scale production runs, offering low per-unit costs, short cycle times, and high throughput rates when used with automated welding systems.
- Repairability: Welding enables the repair and refurbishment of damaged or worn metal components, extending their service life and reducing the need for costly replacements in industrial, automotive, and marine applications.
- Applications:
- Manufacturing: Welding is widely used in manufacturing industries for fabricating metal structures, frames, chassis, and assemblies in automotive, aerospace, shipbuilding, and machinery production.
- Construction: Welding plays a crucial role in construction projects for joining structural steel beams, columns, and trusses, as well as fabricating bridges, pipelines, and other infrastructure components.
- Automotive and Transportation: Welding is employed in the automotive and transportation sectors for assembling vehicle bodies, frames, exhaust systems, and suspension components with high strength and dimensional accuracy.
- Oil and Gas: Welding is essential in the oil and gas industry for constructing pipelines, storage tanks, pressure vessels, and offshore platforms that withstand harsh operating conditions and environmental factors.
- Power Generation: Welding is used in power generation facilities for fabricating boilers, turbines, heat exchangers, and piping systems in fossil fuel, nuclear, and renewable energy plants.
In summary, welding is a versatile and essential metal fabrication process used to join metal parts together in various industries and applications. Its ability to create strong, durable, and reliable bonds makes it indispensable in manufacturing, construction, repair, and maintenance activities, contributing to the development of modern infrastructure and technology.
Plasma Cutting:
Plasma cutting is a metal fabrication process that utilizes a high-velocity jet of ionized gas to cut through electrically conductive materials such as steel, stainless steel, aluminum, copper, and brass. It is widely used in industries requiring high precision and speed for cutting thick metal sheets and plates.
- Principle of Operation:
- Plasma cutting works by passing an electric arc through a gas (typically compressed air, nitrogen, or argon) to create a plasma jet with temperatures exceeding 20,000 degrees Celsius. The intense heat of the plasma jet melts and blows away the metal, creating a narrow kerf width and producing a clean, precise cut.
- The plasma jet is directed through a constricted nozzle at high velocity, focusing the energy and enabling efficient cutting through the material. The workpiece is mounted on a CNC (Computer Numerical Control) table, which moves the cutting torch along programmed paths to achieve the desired cutting shape and dimensions.
- Types of Plasma Cutting Systems:
- Conventional Plasma Cutting: Conventional plasma cutting systems use compressed air as the plasma gas and are suitable for cutting mild steel, stainless steel, and aluminum up to moderate thicknesses (typically up to 25 mm).
- High-Definition Plasma Cutting: High-definition (HD) plasma cutting systems employ advanced torch and nozzle designs, along with optimized gas mixtures (such as nitrogen-hydrogen), to achieve higher cutting speeds, improved edge quality, and tighter tolerances on thinner materials.
- Precision Plasma Cutting: Precision plasma cutting systems utilize finer plasma arcs and narrower kerf widths to achieve superior cut quality and dimensional accuracy on thin gauge materials, such as sheet metal and fine plate.
- CNC Plasma Cutting: CNC plasma cutting machines are equipped with computer-controlled torches and tables, allowing for automated and precise cutting of complex shapes, contours, and patterns from CAD/CAM (Computer-Aided Design/Computer-Aided Manufacturing) files.
- Materials:
- Plasma cutting can be used to cut a wide range of electrically conductive materials, including carbon steel, stainless steel, aluminum, copper, brass, titanium, and their alloys. It is particularly well-suited for cutting thick metal sheets and plates in fabrication, manufacturing, and construction applications.
- Advantages:
- High Speed: Plasma cutting offers high cutting speeds, making it suitable for rapid production and efficient material processing, especially for cutting thick metal sections.
- Versatility: Plasma cutting is versatile and adaptable to a variety of material types, thicknesses, and geometries, allowing for the fabrication of complex parts and assemblies with minimal setup time.
- Precision and Accuracy: Plasma cutting systems can achieve high precision and dimensional accuracy, with the ability to cut intricate shapes, sharp corners, and fine details on metal surfaces.
- Clean Cutting: Plasma cutting produces clean, smooth edges with minimal dross (residual metal) and minimal heat-affected zones, resulting in minimal post-cutting finishing and cleanup requirements.
- Cost-Effectiveness: Plasma cutting is a cost-effective metal cutting method, offering low operating costs, minimal tooling requirements, and high productivity rates compared to alternative cutting processes such as laser cutting or waterjet cutting.
- Applications:
- Metal Fabrication: Plasma cutting is widely used in metal fabrication shops for cutting thick metal plates, sheets, and profiles to create components and structures for various industries, including automotive, aerospace, construction, and machinery manufacturing.
- Construction and Structural Steel: Plasma cutting is employed in construction projects for cutting steel beams, columns, plates, and other structural elements with precision and speed, facilitating the assembly of buildings, bridges, and infrastructure.
- Heavy Equipment Manufacturing: Plasma cutting is utilized in heavy equipment manufacturing for cutting and profiling metal components for machinery, earthmoving equipment, agricultural implements, and mining machinery.
- Shipbuilding and Marine: Plasma cutting plays a vital role in shipbuilding and marine industries for cutting steel plates, hull sections, and structural components for ships, offshore platforms, and marine structures with accuracy and efficiency.
- Metal Art and Sculpture: Plasma cutting is used by artists and sculptors for creating intricate metal artworks, sculptures, signs, and decorative features with custom designs and patterns.
In summary, plasma cutting is a versatile and efficient metal fabrication process used to cut electrically conductive materials with high precision and speed. Its applications span various industries, including metal fabrication, construction, manufacturing, shipbuilding, and art, making it a valuable technology in modern production and design processes.
Waterjet Cutting:
Waterjet cutting is a versatile metal fabrication process that utilizes a high-pressure stream of water mixed with abrasive particles to cut through a wide range of materials, including metals, ceramics, composites, glass, and stone. It is known for its ability to produce clean, precise cuts with minimal heat-affected zones and is widely used in various industries for cutting complex shapes and profiles.
- Principle of Operation:
- Waterjet cutting works by pressurizing water to extremely high levels (typically between 40,000 to 90,000 psi) and then forcing it through a small nozzle at high velocity.
- In abrasive waterjet cutting, abrasive particles (typically garnet) are mixed with the pressurized water stream to enhance cutting efficiency and capability. The abrasive particles act as cutting agents, increasing the cutting power of the waterjet.
- The high-velocity waterjet, combined with abrasive particles, erodes the material being cut, creating a narrow kerf width and producing a smooth, burr-free edge.
- Types of Waterjet Cutting Systems:
- Pure Waterjet Cutting: Pure waterjet cutting systems use only pressurized water to cut soft materials such as rubber, foam, plastics, and thin metals. They are suitable for applications where minimal material damage and heat generation are required.
- Abrasive Waterjet Cutting: Abrasive waterjet cutting systems inject abrasive particles into the water stream to cut harder materials such as metals, ceramics, and composites. They offer higher cutting speeds and are capable of cutting thicker materials compared to pure waterjet systems.
- Materials:
- Waterjet cutting can be used to cut a wide range of materials, including but not limited to:
- Metals: Steel, stainless steel, aluminum, copper, brass, titanium, nickel alloys, and alloys.
- Non-Metals: Glass, ceramics, composites, plastics, rubber, foam, stone, and wood.
- It is particularly well-suited for cutting materials that are sensitive to heat or prone to thermal deformation, as waterjet cutting produces minimal heat-affected zones and does not cause material distortion.
- Advantages:
- Precision and Accuracy: Waterjet cutting offers high precision and dimensional accuracy, with the ability to cut complex shapes, sharp corners, and fine details with tolerances as tight as ±0.1 mm.
- Minimal Heat-Affected Zones: Waterjet cutting produces minimal heat-affected zones (HAZ) and does not induce thermal stress or distortion in the material, making it suitable for cutting heat-sensitive materials and thin sections.
- Versatility: Waterjet cutting is versatile and can cut a wide range of materials, thicknesses, and geometries without the need for specialized tooling or setup changes.
- Burr-Free and Clean Cutting: Waterjet cutting produces clean, burr-free edges without secondary finishing operations, reducing the need for additional machining or deburring processes.
- Environmental Friendliness: Waterjet cutting is an environmentally friendly process as it does not generate hazardous fumes, dust, or by-products, and the abrasive particles can be recycled and reused.
- Applications:
- Metal Fabrication: Waterjet cutting is widely used in metal fabrication shops for cutting metal sheets, plates, tubes, and profiles to create components and assemblies for various industries, including aerospace, automotive, marine, and architecture.
- Precision Engineering: Waterjet cutting is employed in precision engineering and manufacturing industries for producing intricate parts, prototypes, and tooling with tight tolerances and complex geometries.
- Architectural and Decorative: Waterjet cutting is utilized in architectural and decorative applications for cutting intricate patterns, designs, and motifs in metals, glass, stone, and tile for building facades, interior decor, and artistic installations.
- Aerospace and Defense: Waterjet cutting plays a vital role in the aerospace and defense sectors for cutting aerospace-grade materials, composites, and armor plates with high precision and repeatability for aircraft, missiles, and military vehicles.
- Automotive and Motorsports: Waterjet cutting is used in automotive manufacturing and motorsports for cutting chassis components, body panels, engine parts, and composite materials with accuracy and efficiency.
In summary, waterjet cutting is a versatile and precise metal fabrication process that offers high-speed cutting capabilities with minimal heat generation and material distortion. Its applications span various industries, including metal fabrication, aerospace, automotive, architecture, and defense, making it a valuable technology for producing complex parts and components with superior quality and accuracy.
Roll Forming:
Roll forming is a metal fabrication process used to shape flat metal sheets or strips into continuous, uniform profiles and shapes by passing them through a series of rollers. It is commonly used in the production of long-length components with consistent cross-sections and complex geometries.
- Principle of Operation:
- Roll forming operates on the principle of continuous bending and shaping of metal sheets or strips by passing them through a series of consecutive rollers, each of which performs a specific bending or forming operation.
- The metal sheet or strip is fed into the roll forming machine, where it is guided through a series of paired rollers arranged in a sequence of forming stations.
- Each forming station consists of two or more rollers that gradually bend, shape, and deform the metal to achieve the desired profile or cross-section. The rollers are typically contoured to match the shape of the final product.
- The material is progressively shaped as it passes through the forming stations, with each set of rollers incrementally bending and forming the metal until it reaches the end of the roll forming line.
- Types of Roll Forming Machines:
- Single Stand Roll Forming: Single stand roll forming machines consist of a single set of rollers that perform all forming operations in a linear sequence. They are suitable for producing simple profiles and shapes with limited complexity.
- Double Stand Roll Forming: Double stand roll forming machines feature two sets of rollers arranged in tandem, allowing for increased forming flexibility and the production of more complex profiles and shapes in a single pass.
- Continuous Roll Forming: Continuous roll forming machines utilize an endless loop of rollers to continuously feed and form the material, enabling the production of long-length components with uniform profiles and consistent quality.
- Duplex Roll Forming: Duplex roll forming machines consist of two separate roll forming lines operating in parallel, allowing for simultaneous production of two different profiles or configurations.
- Materials:
- Roll forming can be performed on a variety of metallic materials, including steel, stainless steel, aluminum, copper, brass, and their alloys. The material thickness typically ranges from thin gauge sheets (e.g., 0.5 mm) to thicker plates (e.g., 6 mm), depending on the roll forming machine capabilities and requirements.
- Advantages:
- High Efficiency: Roll forming offers high production efficiency, with the ability to produce long-length components at high speeds and with minimal operator intervention.
- Consistent Quality: Roll forming provides consistent cross-sectional profiles and dimensional accuracy across large production batches, ensuring uniformity and repeatability in the finished products.
- Versatility: Roll forming can produce a wide range of profiles, shapes, and configurations, including open and closed sections, channels, angles, tubes, and custom designs, making it suitable for diverse applications.
- Material Savings: Roll forming minimizes material waste by optimizing the use of flat metal sheets or strips and reducing scrap compared to traditional machining or fabrication methods.
- Cost-Effectiveness: Roll forming is a cost-effective manufacturing process, offering low tooling costs, short setup times, and efficient production rates for both small and large production volumes.
- Applications:
- Construction and Building Systems: Roll forming is widely used in the construction industry for producing structural components, roofing panels, wall cladding systems, purlins, studs, and other building materials with standardized profiles and lengths.
- Automotive and Transportation: Roll forming is employed in automotive manufacturing for fabricating chassis components, frame rails, structural reinforcements, and body panels with tailored profiles and strength characteristics.
- Furniture and Appliances: Roll forming is utilized in furniture and appliance manufacturing for producing metal frames, brackets, trims, and components with customized shapes and configurations for assembly and mounting.
- Solar Energy: Roll forming plays a crucial role in the solar energy industry for producing mounting systems, racks, and frames for solar panels with precise profiles and dimensions to withstand environmental loads and conditions.
- Material Handling and Storage: Roll forming is used in the production of shelving systems, storage racks, conveyor systems, and material handling equipment for warehouses, distribution centers, and industrial facilities.
In summary, roll forming is a versatile and efficient metal fabrication process used to produce continuous profiles and shapes from flat metal sheets or strips. Its applications span various industries, including construction, automotive, furniture, solar energy, and material handling, making it a fundamental technology in modern manufacturing and engineering processes.
Hydroforming:
Hydroforming is a metal fabrication process that utilizes hydraulic pressure to shape and form metal parts into complex geometries using fluid pressure instead of conventional stamping or machining methods. It is commonly used in the automotive, aerospace, and bicycle industries for producing lightweight, structurally efficient components with high strength-to-weight ratios.
- Principle of Operation:
- Hydroforming operates on the principle of utilizing fluid pressure to shape and form metal parts against a die or mold cavity. It involves the use of a hydraulic fluid (usually water or oil) to exert pressure on a metal blank or tube, forcing it to conform to the shape of the die.
- The process typically involves two main methods: sheet hydroforming and tube hydroforming.
- Sheet Hydroforming: In sheet hydroforming, a flat metal sheet is clamped between a die and a flexible diaphragm or bladder. Hydraulic pressure is then applied to the backside of the metal sheet, causing it to deform and take the shape of the die cavity.
- Tube Hydroforming: In tube hydroforming, a hollow metal tube is placed inside a die cavity and sealed at both ends. Hydraulic pressure is applied to the interior of the tube, causing it to expand and conform to the shape of the die, resulting in complex tubular components.
- Types of Hydroforming:
- Conventional Hydroforming: Conventional hydroforming uses a single fluid chamber or bladder to apply pressure uniformly over the entire surface of the metal blank or tube. It is suitable for producing symmetrical and relatively simple shapes.
- Deep Drawing Hydroforming: Deep drawing hydroforming utilizes multiple fluid chambers or bladders positioned strategically to apply differential pressure to specific areas of the metal blank, allowing for the formation of deeper and more complex shapes with varying wall thicknesses.
- Tube Hydroforming: Tube hydroforming is specifically used for shaping hollow metal tubes into complex and lightweight structural components such as bicycle frames, automotive chassis, and aerospace structures. It offers advantages in terms of material utilization, weight reduction, and design flexibility.
- Materials:
- Hydroforming can be performed on a variety of metallic materials, including aluminum, steel, stainless steel, copper, brass, and their alloys. The choice of material depends on factors such as strength requirements, corrosion resistance, and cost considerations.
- Advanced high-strength steels (AHSS) and aluminum alloys are commonly used in automotive hydroforming applications to achieve lightweighting objectives while maintaining structural integrity and crashworthiness.
- Advantages:
- Complex Geometries: Hydroforming enables the production of complex and intricate part geometries with smooth contours, sharp corners, and deep draws that are difficult or impossible to achieve with conventional stamping or machining methods.
- Lightweight Design: Hydroforming allows for the optimization of material distribution and wall thickness, resulting in lightweight and structurally efficient components that offer improved fuel efficiency, performance, and sustainability.
- Reduced Tooling Costs: Hydroforming requires fewer tooling components compared to traditional stamping methods, as it relies on a single die cavity and flexible bladder or chamber, leading to reduced tooling costs and shorter lead times for new part development.
- Improved Material Utilization: Hydroforming minimizes material waste by using flat or tubular metal blanks more efficiently and reducing scrap generation compared to traditional stamping or machining processes.
- Enhanced Strength and Durability: Hydroformed components exhibit superior strength, stiffness, and fatigue resistance due to the uniform grain structure and work-hardened properties resulting from the forming process, leading to increased part longevity and reliability.
- Applications:
- Automotive Industry: Hydroforming is widely used in the automotive industry for producing structural components such as frame rails, engine cradles, suspension arms, and crash beams, as well as body-in-white (BIW) components such as A-pillars, B-pillars, and roof rails.
- Aerospace and Defense: Hydroforming is employed in the aerospace and defense sectors for fabricating aircraft fuselage structures, wing components, fuel tanks, and missile casings with optimized weight, strength, and aerodynamic performance.
- Bicycle Manufacturing: Hydroforming is extensively used in the bicycle industry for creating lightweight and rigid frame tubes, seat tubes, top tubes, and down tubes with custom shapes and profiles to enhance ride quality, stiffness, and aesthetics.
- HVAC and Appliance Industry: Hydroforming is utilized in the HVAC (Heating, Ventilation, and Air Conditioning) and appliance industries for producing heat exchanger components, refrigeration tubing, and appliance enclosures with improved efficiency and durability.
- Sporting Goods and Recreation: Hydroforming is applied in the production of sporting goods and recreational equipment such as golf club shafts, tennis racket frames, ski poles, and motorcycle frames, offering lightweight and high-performance solutions for athletes and enthusiasts.
In summary, hydroforming is a versatile and advanced metal fabrication process that offers significant advantages in terms of design flexibility, lightweight construction, material efficiency, and part performance. Its applications span various industries, including automotive, aerospace, bicycle manufacturing, HVAC, and sporting goods, making it a key technology in the production of complex and lightweight components for modern applications.
Metal Spinning
Metal spinning, also known as spin forming or metal turning, is a metalworking process used to form symmetrical, axisymmetric shapes from flat metal discs or sheets by rotating them on a spinning lathe while applying pressure with specialized tools. It is commonly used for producing hollow metal parts such as bowls, cones, cylinders, and domes with precise dimensions and smooth surfaces.
- Principle of Operation:
- Metal spinning operates on the principle of utilizing a spinning lathe to rotate a metal blank while shaping it with hand-held or automated tools. The metal blank, typically in the form of a flat disc or sheet, is clamped to a rotating mandrel or chuck.
- As the metal blank rotates, pressure is applied to it using specialized forming tools, known as rollers, pucks, or mandrels, which gradually shape the metal into the desired form. The shaping tools are guided manually or by computer-controlled mechanisms to achieve the desired profile.
- The metal spinning process can be performed in various configurations, including hand spinning, manual lathe spinning, semi-automatic spinning, and CNC (Computer Numerical Control) spinning, depending on the complexity of the part and the required precision.
- Types of Metal Spinning:
- Hand Spinning: Hand spinning is the traditional method of metal spinning where skilled craftsmen manually shape the metal blank using hand-held tools and techniques. It offers flexibility and versatility for producing custom parts with unique shapes and profiles.
- Manual Lathe Spinning: Manual lathe spinning utilizes a manually operated lathe machine equipped with forming tools and accessories for shaping metal blanks into symmetrical shapes. It is suitable for low-volume production and prototype development.
- Semi-Automatic Spinning: Semi-automatic spinning involves the use of a semi-automated lathe machine equipped with motorized tooling and controls for automating certain aspects of the spinning process, such as rotation speed and tool movement.
- CNC Spinning: CNC spinning employs computer-controlled lathes with programmable axes and tooling to automate the spinning process and achieve high precision and repeatability. It is ideal for high-volume production runs and complex part geometries.
- Materials:
- Metal spinning can be performed on a variety of ductile materials, including aluminum, stainless steel, copper, brass, bronze, titanium, and their alloys. The choice of material depends on factors such as strength requirements, corrosion resistance, and surface finish specifications.
- Thin gauge materials (typically 0.5 mm to 6 mm thickness) are commonly used in metal spinning due to their formability and ease of shaping.
- Advantages:
- Design Flexibility: Metal spinning offers design flexibility, allowing for the production of complex and symmetrical shapes with minimal tooling investment. It can accommodate various part geometries, including domes, cones, cylinders, hemispheres, and custom profiles.
- Cost-Effectiveness: Metal spinning is a cost-effective manufacturing process, requiring simple tooling and setup, and offering low production costs for both small and large batch sizes. It is well-suited for prototyping, custom fabrication, and short production runs.
- High Precision: Metal spinning provides high precision and dimensional accuracy, with the ability to achieve tight tolerances and consistent part dimensions across multiple production batches. It is suitable for applications requiring precise fit and finish.
- Smooth Surface Finish: Metal spinning produces parts with smooth surface finishes and uniform wall thickness, eliminating the need for secondary machining or finishing operations. The resulting parts have aesthetically pleasing appearances and enhanced functional properties.
- Material Utilization: Metal spinning optimizes material utilization by minimizing waste and scrap generation, as the entire blank is formed into the final shape without material loss. It is environmentally friendly and resource-efficient compared to other metal forming methods.
- Applications:
- Lighting and Lampshades: Metal spinning is widely used in the lighting industry for producing lampshades, reflectors, and decorative lighting fixtures with customized shapes and finishes.
- Aerospace and Aviation: Metal spinning is employed in the aerospace and aviation sectors for manufacturing components such as engine housings, missile nose cones, satellite dishes, and fuel tanks with lightweight and aerodynamic designs.
- Automotive Parts: Metal spinning is utilized in the automotive industry for producing exhaust components, wheel covers, fuel caps, and decorative trim elements with precise dimensions and surface finishes.
- Kitchenware and Cookware: Metal spinning is applied in the production of kitchenware and cookware items such as pots, pans, bowls, and utensils with smooth surfaces, uniform thickness, and ergonomic designs.
- Architectural and Decorative Elements: Metal spinning is used in architectural and decorative applications for creating ornamental elements, columns, spires, and custom signage with intricate designs and patterns.
In summary, metal spinning is a versatile and efficient metalworking process used to produce axisymmetric parts with precision and consistency. Its applications span various industries, including lighting, aerospace, automotive, kitchenware, and architecture, making it a valuable technology for producing custom and high-quality metal components for diverse applications.
Metal Inert Gas (MIG) Welding:
Metal Inert Gas (MIG) welding, also known as Gas Metal Arc Welding (GMAW), is a welding process that uses a consumable electrode wire and a shielding gas to join metal workpieces. It is one of the most widely used welding processes in industrial applications due to its versatility, efficiency, and ease of automation.
- Principle of Operation:
- MIG welding operates on the principle of creating an electric arc between a continuous solid wire electrode and the workpiece. The electrode wire is fed through a welding gun and melts into the weld pool, joining the base metals together.
- A shielding gas, typically a mixture of argon and carbon dioxide or argon and oxygen, is fed through the welding gun to protect the molten weld pool from atmospheric contamination and oxidation. The shielding gas forms a protective atmosphere around the arc, ensuring clean and sound welds.
- The welding parameters, including voltage, current, wire feed speed, and shielding gas composition, are controlled by the welding power source and can be adjusted to accommodate different material types, thicknesses, and joint configurations.
- Equipment:
- Welding Power Source: The welding power source provides the electrical energy necessary to create the welding arc and regulate the welding parameters. It can be a constant voltage (CV) or constant current (CC) type, depending on the welding process and application requirements.
- Wire Feeder: The wire feeder mechanism delivers the electrode wire from a spool to the welding gun at a controlled rate. It ensures consistent wire feed speed and smooth operation during welding.
- Welding Gun: The welding gun houses the electrode wire and shielding gas nozzle. It provides the means to control the arc length, direct the weld bead, and deliver the shielding gas to the weld area.
- Shielding Gas Supply: The shielding gas supply system delivers the appropriate mixture of inert gases to the welding gun, ensuring adequate coverage of the weld pool and protection against atmospheric contamination.
- Materials:
- MIG welding can be used to join a wide range of ferrous and non-ferrous metals, including carbon steel, stainless steel, aluminum, copper, brass, and their alloys. It is suitable for welding materials of varying thicknesses, from thin sheet metal to thick plates.
- Advantages:
- High Productivity: MIG welding offers high deposition rates and fast welding speeds, resulting in increased productivity and reduced welding cycle times compared to other welding processes.
- Versatility: MIG welding is versatile and can be used to weld a wide variety of materials, joint configurations, and thicknesses. It is suitable for both manual and automated welding applications.
- All-Position Welding: MIG welding can be performed in all welding positions, including flat, horizontal, vertical, and overhead, providing flexibility and accessibility in various fabrication scenarios.
- Minimal Weld Defects: MIG welding produces welds with minimal spatter, porosity, and distortion when performed correctly, resulting in high-quality and visually appealing welds.
- Ease of Use: MIG welding is relatively easy to learn and operate, making it suitable for welders of all skill levels. It requires minimal post-weld cleaning and finishing, reducing overall fabrication time and costs.
- Applications:
- Automotive Industry: MIG welding is extensively used in the automotive industry for joining body panels, chassis components, exhaust systems, and structural assemblies. It offers high weld quality, structural integrity, and production efficiency in mass production environments.
- Fabrication and Manufacturing: MIG welding is employed in various fabrication and manufacturing processes, including metal furniture production, equipment manufacturing, structural steel fabrication, and general metalwork.
- Construction and Infrastructure: MIG welding is utilized in the construction and infrastructure sectors for welding structural steel beams, columns, pipes, and fittings for buildings, bridges, pipelines, and other infrastructure projects.
- Aerospace and Defense: MIG welding plays a crucial role in the aerospace and defense industries for welding aircraft structures, fuselage components, fuel tanks, and missile casings with stringent quality and performance requirements.
- Shipbuilding and Marine: MIG welding is used in shipbuilding and marine applications for welding hull structures, decks, bulkheads, and piping systems in commercial vessels, naval ships, and offshore platforms.
In summary, Metal Inert Gas (MIG) welding is a versatile and widely used welding process that offers high productivity, versatility, and weld quality for joining a wide range of metal materials in various industries. Its applications span automotive, fabrication, construction, aerospace, marine, and many other sectors, making it an indispensable technology in modern manufacturing and fabrication processes.
Tungsten Inert Gas (TIG) Welding:
Tungsten Inert Gas (TIG) welding, also known as Gas Tungsten Arc Welding (GTAW), is an arc welding process that uses a non-consumable tungsten electrode and a shielding gas to join metal workpieces. TIG welding is highly versatile and is commonly used for welding thin materials, precision welding, and welding exotic metals.
- Principle of Operation:
- TIG welding operates on the principle of creating an electric arc between a non-consumable tungsten electrode and the workpiece. Unlike MIG welding, the tungsten electrode does not melt during the welding process, making it a non-consumable electrode.
- A shielding gas, typically argon or helium, is fed through the welding torch to protect the weld pool and tungsten electrode from atmospheric contamination and oxidation. The shielding gas forms a stable arc and provides a clean welding environment.
- Filler metal may be added manually to the weld joint in the form of a separate wire rod if additional material is required to fill gaps or build up weld metal.
- Equipment:
- Welding Power Source: The welding power source provides the electrical energy necessary to create and sustain the welding arc. It controls the welding parameters such as arc voltage, current, and pulse settings.
- TIG Welding Torch: The TIG welding torch holds the non-consumable tungsten electrode and directs the flow of shielding gas to the weld area. It may also include controls for adjusting welding parameters and feeding filler metal.
- Tungsten Electrode: The tungsten electrode is a non-consumable electrode used to initiate and maintain the welding arc. It is made of pure tungsten or a tungsten alloy and is available in various sizes and configurations for different welding applications.
- Shielding Gas Supply: The shielding gas supply system delivers the appropriate gas mixture (argon, helium, or a combination) to the welding torch to protect the weld pool and tungsten electrode from atmospheric contamination.
- Materials:
- TIG welding is suitable for welding a wide range of metals and alloys, including carbon steel, stainless steel, aluminum, copper, titanium, nickel alloys, and exotic metals such as magnesium and zirconium.
- It is particularly well-suited for welding thin materials and non-ferrous metals due to its precise control and low heat input.
- Advantages:
- Precision and Control: TIG welding offers precise control over the welding arc, heat input, and filler metal deposition, making it ideal for welding thin materials, intricate components, and precision parts with tight tolerances.
- High-Quality Welds: TIG welding produces high-quality welds with minimal spatter, distortion, and defects. The stable arc and precise control over welding parameters result in clean, uniform weld beads with excellent mechanical properties.
- Versatility: TIG welding is versatile and can be used to weld a wide variety of metals and alloys in various thicknesses and configurations. It is suitable for both manual and automated welding applications.
- No Flux Required: TIG welding does not require flux to protect the weld pool, as the shielding gas provides ample protection against atmospheric contamination. This eliminates the need for post-weld cleaning and reduces the risk of weld contamination.
- Aesthetic Appearance: TIG welding produces aesthetically pleasing welds with smooth, shiny surfaces and minimal discoloration. It is often used in applications where weld appearance is important, such as architectural, automotive, and decorative welding.
- Applications:
- Aerospace and Aviation: TIG welding is widely used in the aerospace and aviation industries for welding aircraft components, engine parts, fuel tanks, and structural assemblies. It offers precise control, high-quality welds, and compatibility with aerospace-grade materials.
- Nuclear and Power Generation: TIG welding is employed in the nuclear and power generation sectors for welding critical components such as pressure vessels, piping systems, heat exchangers, and turbine blades. It ensures high integrity welds and meets stringent quality standards.
- Pharmaceutical and Food Industry: TIG welding is utilized in the pharmaceutical and food processing industries for welding stainless steel components such as tanks, vessels, and pipelines. It produces clean, sanitary welds with minimal contamination and porosity.
- Automotive and Motorsports: TIG welding is used in automotive manufacturing and motorsports for welding exhaust systems, roll cages, chassis components, and suspension parts. It offers lightweight construction, high strength, and precision welding capabilities.
- Precision Fabrication: TIG welding is employed in precision fabrication and manufacturing industries for welding precision components, instrumentation, medical devices, and laboratory equipment. It enables intricate welds with minimal distortion and heat-affected zones.
In summary, Tungsten Inert Gas (TIG) welding is a versatile and precise welding process that offers high-quality welds, precise control, and compatibility with a wide range of materials. Its applications span various industries, including aerospace, power generation, automotive, pharmaceuticals, and precision fabrication, making it a fundamental technology in modern welding and manufacturing processes.
Submerged Arc Welding (SAW):
Submerged Arc Welding (SAW) is a welding process that uses a continuous wire electrode and a granular flux to create welds. It is characterized by the formation of a submerged arc between the electrode and the workpiece, which is shielded by a blanket of granular flux. SAW is known for its high deposition rates, deep penetration capabilities, and suitability for welding thick materials.
- Principle of Operation:
- Submerged Arc Welding (SAW) operates on the principle of creating an arc between a continuously fed wire electrode and the workpiece. The arc is submerged beneath a layer of granular flux, which shields the arc and molten weld pool from atmospheric contamination.
- The electrode is fed automatically from a spool through a welding head or torch and into the weld joint. The arc melts both the electrode wire and the base metal, forming a molten weld pool that solidifies to create the weld joint.
- The granular flux serves multiple purposes, including generating a protective gas shield, stabilizing the arc, facilitating slag removal, and controlling the weld bead profile. It also provides additional alloying elements to the weld metal, improving mechanical properties and weld quality.
- Equipment:
- Welding Power Source: The welding power source provides the electrical energy necessary to create and maintain the welding arc. It controls welding parameters such as voltage, current, and wire feed speed to optimize weld quality and performance.
- Welding Head or Torch: The welding head or torch holds the electrode wire and directs it into the weld joint. It may also include provisions for flux delivery, arc monitoring, and weld seam tracking.
- Wire Feeder: The wire feeder mechanism delivers the electrode wire from a spool to the welding head at a controlled rate. It ensures consistent wire feed speed and smooth operation during welding.
- Flux Hopper: The flux hopper stores and dispenses the granular flux onto the weld joint, creating a protective layer that shields the arc and weld pool from atmospheric contamination.
- Materials:
- Submerged Arc Welding (SAW) is commonly used for welding medium to heavy thickness materials, typically ranging from 5 mm to 50 mm or more. It is suitable for welding a wide range of ferrous and non-ferrous metals, including carbon steel, low-alloy steel, stainless steel, nickel alloys, and high-strength steels.
- SAW is particularly well-suited for welding materials that require high deposition rates, deep penetration, and consistent weld quality in thick sections.
- Advantages:
- High Deposition Rates: Submerged Arc Welding (SAW) offers exceptionally high deposition rates, allowing for rapid welding of thick materials and large weld joints. It is well-suited for high-volume production and fabrication of heavy structures.
- Deep Penetration: SAW provides deep penetration into the base metal, resulting in strong, fully penetrated welds with excellent fusion and mechanical properties. It is ideal for welding thick materials and achieving full joint penetration in single pass welds.
- Minimal Spatter: SAW produces minimal spatter compared to other welding processes, leading to cleaner welds and reduced post-weld cleanup. The submerged arc and granular flux create a stable arc and protect the weld pool from atmospheric contamination.
- Operator Efficiency: SAW can be highly automated, allowing for continuous, long-duration welding operations with minimal operator intervention. It is suitable for mechanized and robotic welding systems, reducing labor costs and increasing productivity.
- Weld Quality and Consistency: SAW produces high-quality welds with consistent bead profiles, excellent fusion characteristics, and minimal defects such as porosity and slag inclusions. It is well-suited for critical applications requiring reliable and structurally sound welds.
- Applications:
- Heavy Fabrication: Submerged Arc Welding (SAW) is widely used in heavy fabrication industries such as shipbuilding, offshore structures, pressure vessel manufacturing, and bridge construction. It is employed for welding thick plates, beams, columns, and structural components with high strength and integrity.
- Pipe Welding: SAW is commonly used for welding longitudinal and circumferential seams in large-diameter pipes and pipelines for oil and gas transmission, water distribution, and industrial piping systems. It offers high-speed welding and consistent quality in pipe manufacturing.
- Railcar Manufacturing: SAW is utilized in the fabrication of railcars, locomotives, and railway infrastructure for welding structural components, chassis frames, and tank car bodies. It provides efficient, high-strength welds for heavy-duty rail transport applications.
- Weld Overlay Cladding: SAW is employed for weld overlay cladding applications, where a corrosion-resistant alloy is deposited onto the surface of a base metal to provide protection against wear, erosion, and corrosion in harsh environments. It is used in the oil and gas, petrochemical, and power generation industries.
- Wind Tower Fabrication: SAW is used in the fabrication of wind turbine towers and components for welding tower sections, flanges, and transition pieces. It offers high productivity and weld quality in the production of large-scale wind energy structures.
In summary, Submerged Arc Welding (SAW) is a versatile and efficient welding process that offers high deposition rates, deep penetration capabilities, and excellent weld quality for welding thick materials in heavy fabrication, pipeline, railcar, and wind energy applications. Its ability to provide high-speed, high-strength welds makes it a preferred choice for welding large structures and components in various industrial sectors.
Shielded Metal Arc Welding (SMAW):
Shielded Metal Arc Welding (SMAW), commonly known as stick welding or manual metal arc welding (MMA), is a welding process that uses a flux-coated electrode to create an arc between the electrode and the workpiece. It is one of the oldest and most widely used welding processes, known for its simplicity, versatility, and ability to weld in various positions and environments.
- Principle of Operation:
- Shielded Metal Arc Welding (SMAW) operates on the principle of creating an electric arc between a flux-coated electrode and the workpiece. The arc generates intense heat, melting both the electrode and the base metal, forming a weld pool.
- The flux coating on the electrode vaporizes during welding, creating a shielding gas that protects the molten weld pool from atmospheric contamination and oxidation. It also forms a slag layer on the surface of the weld, which helps to cool and solidify the weld metal and protect it from atmospheric exposure.
- The electrode is consumed as it is melted during welding, providing both the filler metal and the flux needed for the weld. The slag layer is removed after welding to reveal the completed weld joint.
- Equipment:
- Welding Power Source: The welding power source provides the electrical energy necessary to create and maintain the welding arc. It controls welding parameters such as voltage, current, and polarity to optimize weld quality and performance.
- Welding Electrode: The welding electrode is a consumable metal rod coated with a flux material. It serves as both the filler metal and the flux source during welding, providing material for the weld joint and generating a protective shielding gas.
- Electrode Holder: The electrode holder, also known as a stinger or clamp, holds the welding electrode and connects it to the welding power source. It allows the welder to manipulate the electrode and control the arc during welding.
- Welding Shield: The welding shield, typically a handheld or helmet-mounted device, protects the welder’s eyes and face from the intense light and heat generated by the welding arc. It may include a darkened lens to filter out harmful ultraviolet (UV) and infrared (IR) radiation.
- Materials:
- Shielded Metal Arc Welding (SMAW) can be used to weld a wide range of ferrous and non-ferrous metals, including carbon steel, stainless steel, cast iron, aluminum, copper, and nickel alloys.
- It is suitable for welding materials of varying thicknesses and compositions, from thin sheet metal to heavy plates and castings.
- Advantages:
- Versatility: Shielded Metal Arc Welding (SMAW) is highly versatile and can be used to weld in various positions, including flat, horizontal, vertical, overhead, and even underwater. It is suitable for both indoor and outdoor welding applications and can be performed in confined spaces.
- Portability: SMAW equipment is relatively compact and portable, making it well-suited for field welding, construction sites, and remote locations where access to power sources may be limited. It does not require external shielding gas or complex setup procedures.
- Simple Setup: SMAW equipment is easy to set up and operate, requiring minimal training and skill to produce sound welds. It does not require elaborate gas supply systems or wire feeding mechanisms, making it accessible to a wide range of users.
- All-Position Welding: SMAW can be performed in all welding positions, offering flexibility and adaptability to different joint configurations and workpiece orientations. It is particularly well-suited for welding vertical and overhead joints where other processes may be more challenging.
- Cost-Effective: SMAW is a cost-effective welding process, requiring minimal equipment investment and maintenance. Electrodes are relatively inexpensive and widely available, making SMAW an economical choice for small-scale fabrication and repair work.
- Applications:
- Construction and Fabrication: Shielded Metal Arc Welding (SMAW) is widely used in the construction industry for welding structural steel beams, columns, bridges, and other infrastructure components. It is also used in metal fabrication shops for welding tanks, frames, and machinery.
- Pipeline Welding: SMAW is commonly used for welding pipelines, both onshore and offshore, for transporting oil, gas, water, and other fluids. It offers versatility, reliability, and accessibility in remote and rugged environments.
- Maintenance and Repair: SMAW is often used for maintenance and repair welding in industries such as manufacturing, mining, agriculture, and automotive. It can be used to repair damaged parts, rebuild worn surfaces, and join dissimilar metals.
- Shipbuilding and Marine: SMAW is employed in shipbuilding and marine applications for welding hull structures, decks, bulkheads, and piping systems. It provides high-strength welds with good impact resistance and corrosion protection.
- Infrastructure and Utilities: SMAW is used in the construction and maintenance of infrastructure and utilities such as bridges, dams, power plants, and water treatment facilities. It is suitable for welding steel and other metals in harsh and corrosive environments.
In summary, Shielded Metal Arc Welding (SMAW) is a versatile and widely used welding process known for its simplicity, versatility, and
Gas Tungsten Arc Welding (GTAW):
Gas Tungsten Arc Welding (GTAW), also known as Tungsten Inert Gas (TIG) welding, is an arc welding process that uses a non-consumable tungsten electrode to produce the weld. GTAW is characterized by its precise control, high-quality welds, and versatility in welding various metals and alloys.
- Principle of Operation:
- Gas Tungsten Arc Welding (GTAW) operates on the principle of creating an electric arc between a non-consumable tungsten electrode and the workpiece. The arc generates intense heat, melting both the base metal and the filler metal (if used), forming a weld pool.
- A shielding gas, typically argon or helium, is fed through the welding torch to protect the weld pool and tungsten electrode from atmospheric contamination and oxidation. The shielding gas also helps to stabilize the arc and provide better arc control.
- The tungsten electrode, which is not consumed during welding, remains at a constant length throughout the process. Filler metal may be added manually to the weld joint as needed to build up the weld or fill gaps.
- Equipment:
- Welding Power Source: The welding power source provides the electrical energy necessary to create and maintain the welding arc. It controls welding parameters such as voltage, current, and pulse settings to optimize weld quality and performance.
- Tungsten Electrode: The tungsten electrode is a non-consumable electrode used to initiate and maintain the welding arc. It is made of pure tungsten or a tungsten alloy and is available in various sizes and configurations for different welding applications.
- Welding Torch: The welding torch holds the tungsten electrode and directs the flow of shielding gas to the weld area. It may include provisions for adding filler metal manually and adjusting welding parameters such as arc length and gas flow rate.
- Shielding Gas Supply: The shielding gas supply system delivers the appropriate gas mixture (argon, helium, or a combination) to the welding torch to protect the weld pool and tungsten electrode from atmospheric contamination.
- Materials:
- Gas Tungsten Arc Welding (GTAW) is suitable for welding a wide range of metals and alloys, including carbon steel, stainless steel, aluminum, titanium, copper, nickel alloys, and exotic metals such as magnesium and zirconium.
- It is particularly well-suited for welding thin materials and non-ferrous metals due to its precise control and low heat input.
- Advantages:
- Precise Control: GTAW offers precise control over the welding arc, heat input, and filler metal deposition, making it ideal for welding thin materials, intricate components, and precision parts with tight tolerances.
- High-Quality Welds: GTAW produces high-quality welds with minimal spatter, distortion, and defects. The stable arc and precise control over welding parameters result in clean, uniform weld beads with excellent mechanical properties.
- Versatility: GTAW is versatile and can be used to weld a wide variety of metals and alloys in various thicknesses and configurations. It is suitable for both manual and automated welding applications.
- Clean and Tidy: GTAW produces clean and tidy welds with minimal contamination and discoloration, making it suitable for applications where weld appearance is important, such as architectural, automotive, and decorative welding.
- All-Position Welding: GTAW can be performed in all welding positions, offering flexibility and adaptability to different joint configurations and workpiece orientations. It is particularly well-suited for welding vertical and overhead joints where other processes may be more challenging.
- Applications:
- Aerospace and Aviation: GTAW is widely used in the aerospace and aviation industries for welding aircraft components, engine parts, fuel tanks, and structural assemblies. It offers precise control, high-quality welds, and compatibility with aerospace-grade materials.
- Nuclear and Power Generation: GTAW is employed in the nuclear and power generation sectors for welding critical components such as pressure vessels, piping systems, heat exchangers, and turbine blades. It ensures high integrity welds and meets stringent quality standards.
- Pharmaceutical and Food Industry: GTAW is utilized in the pharmaceutical and food processing industries for welding stainless steel components such as tanks, vessels, and pipelines. It produces clean, sanitary welds with minimal contamination and porosity.
- Automotive and Motorsports: GTAW is used in automotive manufacturing and motorsports for welding exhaust systems, roll cages, chassis components, and suspension parts. It offers lightweight construction, high strength, and precision welding capabilities.
- Precision Fabrication: GTAW is employed in precision fabrication and manufacturing industries for welding precision components, instrumentation, medical devices, and laboratory equipment. It enables intricate welds with minimal distortion and heat-affected zones.
In summary, Gas Tungsten Arc Welding (GTAW) is a versatile and precise welding process that offers high-quality welds, precise control, and compatibility with a wide range of materials. Its applications span various industries, including aerospace, power generation
Flux-Cored Arc Welding (FCAW):
Flux-Cored Arc Welding (FCAW) is a semi-automatic or automatic arc welding process that uses a tubular electrode filled with flux to create the weld. FCAW is known for its high deposition rates, deep penetration capabilities, and suitability for welding thick materials in various positions.
Metal Inert Gas (MIG) Welding:
Metal Inert Gas (MIG) welding, also known as Gas Metal Arc Welding (GMAW), is a welding process that uses a continuous solid wire electrode and an inert gas, typically argon or a mixture of argon and carbon dioxide, to create the weld. MIG welding is widely used in manufacturing, construction, automotive, and other industries for its versatility, speed, and ease of use.
- Principle of Operation:
- Metal Inert Gas (MIG) welding operates on the principle of creating an electric arc between a continuously fed solid wire electrode and the workpiece. The arc generates intense heat, melting both the electrode and the base metal, forming a weld pool.
- An inert gas, such as argon or a mixture of argon and carbon dioxide, is fed through the welding torch to protect the weld pool from atmospheric contamination and oxidation. The shielding gas also helps to stabilize the arc and provide better arc control.
- The solid wire electrode is continuously fed from a spool through the welding torch and into the weld joint. The welding machine controls the wire feed speed, voltage, and current to optimize weld quality and performance.
- Equipment:
- Welding Power Source: The welding power source provides the electrical energy necessary to create and maintain the welding arc. It controls welding parameters such as voltage, current, and wire feed speed to optimize weld quality and performance.
- Wire Feeder: The wire feeder mechanism delivers the solid wire electrode from a spool to the welding torch at a controlled rate. It ensures consistent wire feed speed and smooth operation during welding.
- Welding Torch: The welding torch holds the solid wire electrode and directs the flow of shielding gas to the weld area. It may include provisions for adjusting welding parameters such as arc length, wire feed speed, and gas flow rate.
- Shielding Gas Supply: The shielding gas supply system delivers the appropriate gas mixture to the welding torch to protect the weld pool from atmospheric contamination.
- Materials:
- Metal Inert Gas (MIG) welding is suitable for welding a wide range of ferrous and non-ferrous metals, including carbon steel, stainless steel, aluminum, copper, and various alloys.
- It is particularly well-suited for welding thin materials and for applications where high productivity and weld quality are required.
- Advantages:
- High Productivity: MIG welding offers high deposition rates and faster welding speeds compared to some other welding processes, making it suitable for high-volume production and fabrication.
- Ease of Use: MIG welding is relatively easy to learn and requires minimal operator skill, making it accessible to a wide range of users. The continuous wire feeding mechanism and automatic gas shielding simplify the welding process.
- Versatility: MIG welding can be used to weld a variety of metals and alloys in various thicknesses and configurations. It is suitable for both manual and automated welding applications.
- Clean Welds: MIG welding produces clean, uniform welds with minimal spatter and distortion. The shielding gas provides excellent protection against atmospheric contamination, resulting in high-quality welds with good mechanical properties.
- All-Position Welding: MIG welding can be performed in all welding positions, including flat, horizontal, vertical, and overhead, offering flexibility and adaptability to different joint configurations and workpiece orientations.
- Applications:
- Automotive Manufacturing: MIG welding is widely used in the automotive industry for welding vehicle frames, body panels, exhaust systems, and other components. It offers high-speed welding and consistent weld quality, meeting the demands of mass production.
- Fabrication and Construction: MIG welding is employed in metal fabrication shops, construction sites, and structural steel fabrication for welding structural components, frames, and assemblies. It provides efficient and cost-effective welding solutions for various construction projects.
- Aerospace and Aviation: MIG welding is used in the aerospace and aviation industries for welding aircraft structures, engine components, and fuel tanks. It offers high-quality welds with excellent mechanical properties and corrosion resistance.
- Shipbuilding and Marine: MIG welding is utilized in shipbuilding and marine applications for welding hulls, decks, bulkheads, and piping systems. It provides strong, durable welds suitable for marine environments.
- General Manufacturing: MIG welding is employed in various manufacturing industries for welding machinery, equipment, appliances, and consumer goods. It offers versatility, speed, and reliability in diverse manufacturing applications.
In summary, Metal Inert Gas (MIG) welding is a versatile and efficient welding process that offers high productivity, ease of use, and excellent weld quality. Its applications span various industries, including automotive, construction, aerospace, marine, and general manufacturing
Submerged Arc Welding (SAW):
Submerged Arc Welding (SAW) is a welding process that utilizes an arc between a continuously fed electrode and the workpiece. The arc is submerged beneath a granular flux layer, which protects the weld pool and prevents atmospheric contamination. SAW is known for its high deposition rates, deep penetration capabilities, and suitability for welding thick materials.
- Principle of Operation:
- Submerged Arc Welding (SAW) operates on the principle of creating an electric arc between a continuously fed bare or flux-cored electrode and the workpiece. The arc generates intense heat, melting both the electrode and the base metal, forming a weld pool.
- A layer of granular flux is deposited on the weld joint before welding. The flux serves multiple purposes, including generating a protective gas shield, stabilizing the arc, controlling the weld bead profile, and facilitating slag removal.
- The arc is completely submerged beneath the flux layer during welding, which shields the weld pool from atmospheric contamination and prevents spatter and fumes from escaping into the surrounding environment.
- Equipment:
- Welding Power Source: The welding power source provides the electrical energy necessary to create and maintain the welding arc. It controls welding parameters such as voltage, current, and wire feed speed to optimize weld quality and performance.
- Welding Head: The welding head holds the welding torch, electrode, and flux delivery system. It directs the flow of flux onto the weld joint and controls the welding parameters such as travel speed, electrode angle, and arc length.
- Flux Hopper: The flux hopper stores and delivers the granular flux to the welding head during welding. It ensures consistent flux coverage and distribution on the weld joint.
- Wire Feeder: The wire feeder mechanism delivers the continuously fed electrode from a spool to the welding head at a controlled rate. It ensures consistent wire feed speed and smooth operation during welding.
- Materials:
- Submerged Arc Welding (SAW) is suitable for welding a wide range of ferrous and non-ferrous metals, including carbon steel, low-alloy steel, stainless steel, nickel alloys, and some non-ferrous alloys.
- It is particularly well-suited for welding thick materials and for applications where high deposition rates and deep penetration are required.
- Advantages:
- High Deposition Rates: Submerged Arc Welding (SAW) offers exceptionally high deposition rates, allowing for rapid welding of thick materials and large weld joints. It is well-suited for high-volume production and fabrication.
- Deep Penetration: SAW provides deep penetration into the base metal, resulting in strong, fully penetrated welds with excellent fusion and mechanical properties. It is ideal for welding thick materials and achieving full joint penetration in single pass welds.
- Minimal Spatter and Fumes: The submerged arc process produces minimal spatter and fumes due to the complete submersion of the arc beneath the flux layer. This results in a clean weld environment and reduces the need for post-weld cleaning and rework.
- Excellent Weld Quality: SAW produces high-quality welds with good bead appearance, uniform fusion, and minimal defects. The granular flux acts as a protective barrier, preventing atmospheric contamination and promoting sound weld formation.
- All-Position Welding: SAW can be performed in all welding positions, including flat, horizontal, vertical, and overhead, offering flexibility and adaptability to different joint configurations and workpiece orientations.
- Applications:
- Heavy Fabrication: Submerged Arc Welding (SAW) is widely used in heavy fabrication industries such as shipbuilding, offshore structures, construction, and bridge construction. It is employed for welding thick plates, beams, columns, and structural components with high strength and integrity.
- Pressure Vessel Manufacturing: SAW is utilized in the manufacturing of pressure vessels, boilers, tanks, and piping systems for the petrochemical, oil and gas, and power generation industries. It provides efficient and cost-effective welding solutions for critical applications.
- Rail and Railroad Construction: SAW is used in the fabrication and repair of railway tracks, switches, and crossings for the railroad and transportation industries. It offers high-speed welding and excellent weld quality for long-lasting rail infrastructure.
- Weld Overlay Cladding: SAW is employed for weld overlay cladding applications, where a corrosion-resistant layer is applied to the surface of a base metal to enhance its performance in corrosive environments. It is used in industries such as oil and gas, chemical processing, and mining.
- Structural Steel Construction: SAW is utilized in the construction of buildings, bridges, and other infrastructure for welding structural components such as beams, columns, trusses, and girders. It provides high-strength welds with good impact resistance and ductility.
In summary, Submerged Arc Welding (SAW) is a versatile and efficient welding process that offers high deposition rates, deep penetration, and excellent weld quality. Its applications span various industries, including heavy fabrication, pressure vessel manufacturing, rail and railroad construction, weld overlay cladding, and structural steel construction.
Resistance Spot Welding:
Resistance spot welding (RSW) is a welding process that joins two or more metal sheets together by applying heat and pressure to localized areas. It is commonly used in the automotive, aerospace, electronics, and appliance industries for its speed, efficiency, and reliability.
- Principle of Operation:
- Resistance spot welding (RSW) operates on the principle of passing an electrical current through the interface of two or more metal sheets to be joined. The resistance at the interface generates heat, melting the metal and forming a weld nugget.
- Electrodes apply pressure to the metal sheets, compressing them together during welding. The combination of heat and pressure causes the molten metal to fuse and solidify, creating a strong weld joint.
- The welding cycle typically consists of several stages, including electrode contact, current flow, heat generation, nugget formation, and cooldown. The duration and intensity of each stage are controlled to optimize weld quality and performance.
- Equipment:
- Welding Machine: The welding machine provides the electrical energy necessary to create the welding current and control the welding parameters such as current, time, and pressure. It may include features such as programmable controls, monitoring systems, and safety interlocks.
- Welding Electrodes: The welding electrodes apply pressure to the metal sheets and conduct the welding current to the weld zone. They are usually made of copper or copper alloys to withstand high currents and minimize electrode wear.
- Welding Controls: The welding controls regulate the welding parameters such as current, time, and pressure to ensure consistent and repeatable weld quality. They may be manual, semi-automatic, or fully automated, depending on the application requirements.
- Cooling System: The cooling system dissipates heat generated during welding and prevents overheating of the electrodes and workpieces. It may include water-cooled electrodes, coolant circulation systems, and temperature sensors to maintain optimal operating conditions.
- Materials:
- Resistance spot welding (RSW) is suitable for welding a wide range of metallic materials, including carbon steel, stainless steel, aluminum, copper, brass, and nickel alloys.
- It is commonly used for welding thin to medium thickness metal sheets in various configurations and surface finishes.
- Advantages:
- High Speed: Resistance spot welding (RSW) is a high-speed welding process that can produce multiple welds in rapid succession. It offers fast cycle times and high production rates, making it suitable for mass production and assembly line applications.
- Efficiency: RSW is an efficient welding process that requires minimal setup time and operator skill. Once the welding parameters are dialed in, it can produce consistent and repeatable welds with minimal variation.
- Minimal Distortion: RSW produces minimal distortion and warpage in the workpieces due to the localized heat input and short welding cycle. It is well-suited for welding thin and lightweight materials without compromising dimensional accuracy.
- Clean and Aesthetic Welds: RSW produces clean and aesthetic welds with minimal spatter, splatter, or flux residues. The weld nuggets are typically small and discrete, resulting in visually appealing weld joints suitable for cosmetic applications.
- Versatility: RSW can be used to weld a wide range of materials, thicknesses, and configurations. It is suitable for welding dissimilar metals, coated or painted surfaces, and pre-assembled components without additional surface preparation.
- Applications:
- Automotive Manufacturing: Resistance spot welding (RSW) is widely used in the automotive industry for welding vehicle body panels, chassis components, structural assemblies, and battery packs. It offers fast and efficient welding solutions for high-volume production.
- Appliance Manufacturing: RSW is employed in the appliance industry for welding components such as refrigerator cabinets, oven panels, washing machine housings, and dishwasher assemblies. It provides strong and durable welds for household appliances.
- Electronics Assembly: RSW is used in electronics manufacturing for welding components such as printed circuit boards, connectors, terminals, and housings. It offers precise and reliable welds without damaging sensitive electronic components.
- Aerospace and Aviation: RSW is utilized in the aerospace and aviation industries for welding aircraft structures, fuselage panels, wing assemblies, and engine components. It meets stringent quality and performance requirements for aerospace applications.
- Metal Fabrication: RSW is employed in various metal fabrication industries for welding sheet metal assemblies, enclosures, enclosures, and enclosures. It offers efficient and cost-effective welding solutions for custom fabrication projects.
In summary, Resistance Spot Welding (RSW) is a versatile and efficient welding process that offers high-speed production, minimal distortion, clean welds, and versatility in materials and applications. Its applications span various industries, including automotive, appliance, electronics, aerospace, and metal fabrication.
Laser Beam Welding (LBW):
Laser Beam Welding (LBW) is a high-energy welding process that uses a concentrated laser beam to melt and fuse metal together. LBW offers precise control, high welding speeds, and minimal heat-affected zones, making it suitable for a wide range of applications in various industries.
- Principle of Operation:
- Laser Beam Welding (LBW) operates on the principle of focusing a highly concentrated laser beam onto the workpiece surface. The intense heat generated by the laser beam melts the metal, forming a weld pool that solidifies to create a fusion bond.
- The laser beam is typically generated by a laser source, such as a solid-state laser, CO2 laser, or fiber laser. The beam is directed onto the workpiece using mirrors or optical systems, allowing for precise control over the welding process.
- LBW can be performed in both autogenous mode (without filler material) and with filler material added manually or automatically to the weld joint. The choice of mode depends on the application requirements and material properties.
- Equipment:
- Laser Source: The laser source generates the high-energy laser beam used for welding. It may be a solid-state laser, CO2 laser, fiber laser, or other types of lasers depending on the application requirements.
- Optics System: The optics system consists of mirrors, lenses, and beam delivery systems that control the direction, focus, and intensity of the laser beam. It allows for precise positioning and manipulation of the laser beam during welding.
- Workpiece Handling System: The workpiece handling system holds and positions the workpieces during welding. It may include fixtures, clamps, and robotic arms for automated welding applications.
- Gas Delivery System: The gas delivery system provides shielding gas, such as argon or helium, to protect the weld pool and laser optics from atmospheric contamination. It helps to maintain a clean and stable welding environment.
- Materials:
- Laser Beam Welding (LBW) is suitable for welding a wide range of metallic materials, including carbon steel, stainless steel, aluminum, titanium, nickel alloys, and other exotic metals.
- It is particularly well-suited for welding thin to medium thickness materials and for applications where precise control and minimal heat input are required.
- Advantages:
- High Precision: Laser Beam Welding (LBW) offers precise control over the welding process, allowing for accurate positioning, depth control, and weld bead geometry. It is capable of producing narrow, deep welds with minimal distortion.
- High Speed: LBW can achieve high welding speeds compared to traditional welding processes, resulting in faster production rates and increased efficiency. It is particularly advantageous for high-volume manufacturing and assembly line applications.
- Minimal Heat Affected Zone (HAZ): LBW generates minimal heat input to the workpiece, resulting in a small heat-affected zone (HAZ) and reduced risk of distortion or metallurgical changes in the base metal. It is suitable for welding heat-sensitive materials and thin sections.
- No Contact: LBW is a non-contact welding process, which eliminates the need for physical contact between the welding tool and the workpiece. This reduces wear and tear on equipment and allows for welding of delicate or complex components.
- Versatility: LBW can be used to weld a wide range of materials and thicknesses, as well as dissimilar materials with different melting points. It is suitable for welding intricate shapes, contours, and joints with high precision and repeatability.
- Applications:
- Automotive Manufacturing: Laser Beam Welding (LBW) is widely used in the automotive industry for welding body panels, chassis components, exhaust systems, and engine parts. It offers high-speed welding, precise control, and minimal distortion.
- Aerospace and Aviation: LBW is employed in the aerospace and aviation industries for welding aircraft structures, engine components, fuel tanks, and propulsion systems. It meets stringent quality and performance requirements for aerospace applications.
- Electronics Assembly: LBW is used in electronics manufacturing for welding components such as circuit boards, connectors, sensors, and enclosures. It offers clean, precise welds without damaging sensitive electronic components.
- Medical Device Manufacturing: LBW is utilized in the medical device industry for welding surgical instruments, implants, and medical equipment. It offers biocompatible welds with high strength and precision.
- Microelectronics and Photonics: LBW is employed in microelectronics and photonics industries for welding semiconductor devices, optical components, and microelectromechanical systems (MEMS). It enables precise joining of miniature components with micron-level accuracy.
In summary, Laser Beam Welding (LBW) is a versatile and precise welding process that offers high precision, high speed, minimal heat input, and versatility in materials and applications. Its applications span various industries, including automotive, aerospace, electronics, medical devices, and microelectronics.
Electron Beam Welding (EBW):
Electron Beam Welding (EBW) is a high-energy welding process that utilizes a focused beam of electrons to join metal components together. EBW offers deep penetration, minimal distortion, and precise control, making it suitable for welding a wide range of materials in various industries.
- Principle of Operation:
- Electron Beam Welding (EBW) operates on the principle of accelerating a beam of high-velocity electrons towards the workpiece. The kinetic energy of the electrons is converted into heat upon impact with the workpiece surface, melting the metal and forming a weld pool.
- The electron beam is generated by an electron gun, which emits electrons under vacuum conditions. The beam is focused and directed onto the workpiece using magnetic lenses and beam deflection systems, allowing for precise control over the welding process.
- EBW can be performed in both vacuum and atmospheric conditions, depending on the application requirements and material properties.
- Equipment:
- Electron Gun: The electron gun generates and emits a beam of high-velocity electrons towards the workpiece. It may include cathodes, anodes, filaments, and electron beam control systems to regulate beam intensity, focus, and direction.
- Beam Focusing System: The beam focusing system consists of magnetic lenses and beam deflection systems that control the trajectory and intensity of the electron beam. It allows for precise positioning and manipulation of the beam during welding.
- Workpiece Handling System: The workpiece handling system holds and positions the workpieces during welding. It may include fixtures, clamps, and robotic arms for automated welding applications.
- Vacuum Chamber (optional): In vacuum EBW, a vacuum chamber is used to maintain low-pressure conditions and remove air and gases that could interfere with the electron beam. It ensures a clean and stable welding environment.
- Materials:
- Electron Beam Welding (EBW) is suitable for welding a wide range of metallic materials, including stainless steel, aluminum, titanium, nickel alloys, refractory metals (e.g., tungsten, molybdenum), and other exotic metals.
- It is particularly well-suited for welding thick materials, dissimilar materials, and materials with high melting points.
- Advantages:
- Deep Penetration: Electron Beam Welding (EBW) offers deep penetration into the base metal, resulting in strong, fully penetrated welds with excellent fusion and mechanical properties. It is capable of welding thick materials in a single pass.
- Minimal Heat Affected Zone (HAZ): EBW generates minimal heat input to the workpiece, resulting in a small heat-affected zone (HAZ) and reduced risk of distortion or metallurgical changes in the base metal. It is suitable for welding heat-sensitive materials and critical components.
- High Precision: EBW offers precise control over the welding process, allowing for accurate positioning, depth control, and weld bead geometry. It is capable of producing narrow, deep welds with micron-level accuracy.
- Vacuum Welding Capability: EBW can be performed in vacuum conditions, which eliminates the need for shielding gas and prevents atmospheric contamination of the weld. Vacuum welding reduces the risk of porosity, oxidation, and other defects in the weld joint.
- Versatility: EBW can be used to weld a wide range of materials and thicknesses, as well as dissimilar materials with different melting points. It is suitable for welding intricate shapes, contours, and joints with high precision and repeatability.
- Applications:
- Aerospace and Aviation: Electron Beam Welding (EBW) is widely used in the aerospace and aviation industries for welding aircraft structures, engine components, turbine blades, rocket nozzles, and space vehicle components. It offers high-strength welds with minimal distortion and heat input.
- Medical Device Manufacturing: EBW is utilized in the medical device industry for welding surgical instruments, implants, and medical equipment. It offers biocompatible welds with high strength and precision, meeting stringent quality and regulatory requirements.
- Automotive Manufacturing: EBW is employed in the automotive industry for welding transmission components, drive shafts, engine blocks, and chassis components. It offers high-speed welding, precise control, and minimal distortion for critical automotive applications.
- Nuclear Power Generation: EBW is used in the nuclear power generation industry for welding reactor components, pressure vessels, steam generators, and fuel assemblies. It provides high-integrity welds with minimal risk of radioactive contamination.
- Semiconductor Manufacturing: EBW is employed in the semiconductor industry for welding vacuum chambers, electron beam lithography systems, and other precision equipment. It offers clean, high-vacuum welds with minimal impurities for semiconductor manufacturing processes.
In summary, Electron Beam Welding (EBW) is a versatile and precise welding process that offers deep penetration, minimal heat input, and high precision. Its applications span various industries, including aerospace, medical devices, automotive, nuclear power generation, and semiconductor manufacturing.
Friction Stir Welding (FSW):
Friction Stir Welding (FSW) is a solid-state welding process that joins materials without melting the base metal. FSW is particularly suitable for joining materials that are difficult to weld using conventional fusion welding techniques, such as aluminum, copper, and other non-ferrous alloys.
- Principle of Operation:
- Friction Stir Welding (FSW) operates on the principle of frictional heat generation and plastic deformation. A rotating tool with a specially designed pin or probe is plunged into the joint between the workpieces.
- As the tool rotates and moves along the joint line, it generates frictional heat and mechanical pressure, softening the material and creating a plasticized zone. The rotating tool stirs the plasticized material, mixing the base metal and forming a solid-state weld.
- FSW is conducted at temperatures below the melting point of the base metal, resulting in minimal distortion, reduced heat-affected zones, and superior mechanical properties in the weld joint.
- Equipment:
- Friction Stir Welding Machine: The FSW machine consists of a rigid frame, a workpiece clamping system, a tool holder, and a spindle drive mechanism. It provides the necessary rigidity, stability, and control for the welding process.
- FSW Tool: The FSW tool is the key component of the process and consists of a rotating pin or probe and a shoulder. The tool material is typically made of high-strength tool steel, tungsten carbide, or other wear-resistant alloys.
- Tool Holder: The tool holder secures the FSW tool in place and provides the necessary support and alignment during welding. It may include provisions for adjusting tool position, tilt angle, and plunge depth.
- Cooling System: The cooling system dissipates heat generated during welding and prevents overheating of the FSW tool and workpieces. It may include water-cooled tooling components, coolant circulation systems, and temperature sensors.
- Materials:
- Friction Stir Welding (FSW) is suitable for welding a wide range of metallic materials, including aluminum, magnesium, copper, titanium, steel, and their alloys.
- It is particularly well-suited for welding materials that are difficult to weld using conventional fusion welding techniques, such as high-strength aluminum alloys and dissimilar metal combinations.
- Advantages:
- Solid-State Welding: Friction Stir Welding (FSW) is a solid-state welding process that does not involve melting of the base metal. It produces welds with minimal porosity, solidification defects, and metallurgical changes, resulting in superior mechanical properties and corrosion resistance.
- Minimal Distortion: FSW generates minimal heat input to the workpiece, resulting in reduced distortion and warpage in the weld joint. It is particularly advantageous for welding thin and lightweight materials without compromising dimensional accuracy.
- No Fumes or Spatter: FSW produces no fumes, spatter, or arc radiation, creating a clean and safe working environment for operators. It eliminates the need for shielding gases, fluxes, or consumable filler materials, reducing process complexity and cost.
- Versatility: FSW can be used to weld a wide range of materials and thicknesses, as well as dissimilar materials with different melting points. It is suitable for welding complex geometries, curved surfaces, and irregular joint configurations with high precision and repeatability.
- Environmentally Friendly: FSW is an environmentally friendly welding process that consumes less energy, produces fewer emissions, and generates less waste compared to conventional fusion welding techniques. It is increasingly used in green manufacturing and sustainable engineering applications.
- Applications:
- Aerospace Manufacturing: Friction Stir Welding (FSW) is widely used in the aerospace industry for welding aircraft fuselage panels, wing skins, engine components, and structural assemblies. It offers high-strength welds with excellent fatigue resistance and damage tolerance.
- Automotive Fabrication: FSW is employed in the automotive industry for welding car body panels, chassis components, battery enclosures, and heat exchangers. It provides lightweight, durable welds with improved crashworthiness and fuel efficiency.
- Shipbuilding and Marine Engineering: FSW is utilized in shipbuilding and marine engineering for welding hull panels, deck structures, bulkheads, and pipe joints. It offers corrosion-resistant welds with superior mechanical properties for maritime applications.
- Rail and Transportation: FSW is used in the rail and transportation industries for welding railway tracks, tram components, and lightweight structures. It provides strong, vibration-resistant welds suitable for high-speed rail and urban transit systems.
- Renewable Energy: FSW is employed in the renewable energy sector for welding wind turbine towers, solar panel frames, and tidal energy systems. It offers high-strength welds with excellent fatigue resistance and long-term durability in harsh environmental conditions.
In summary, Friction Stir Welding (FSW) is a versatile and environmentally friendly welding process that offers solid-state joining, minimal distortion, and superior mechanical properties. Its applications span various industries, including aerospace, automotive, marine, rail, and renewable energy.
Gas Metal Arc Welding (GMAW), also known as MIG welding:
Gas Metal Arc Welding (GMAW), commonly referred to as MIG (Metal Inert Gas) welding, is a welding process that uses a consumable wire electrode and an inert gas to shield the weld pool from atmospheric contamination. GMAW is widely used in various industries due to its versatility, high welding speed, and ease of automation.
- Principle of Operation:
- Gas Metal Arc Welding (GMAW) operates on the principle of creating an electric arc between a continuously fed consumable wire electrode and the workpiece. The arc generates intense heat, melting both the electrode wire and the base metal, forming a weld pool.
- An inert gas, such as argon, helium, or a mixture of gases, is continuously fed through the welding gun to shield the weld pool from atmospheric contamination. The gas also helps to stabilize the arc and improve weld quality.
- GMAW can be performed in various modes, including short-circuiting transfer, globular transfer, spray transfer, and pulsed spray transfer, depending on the welding parameters and application requirements.
- Equipment:
- Welding Power Source: The welding power source provides the electrical energy necessary to create and maintain the welding arc. It controls welding parameters such as voltage, current, and wire feed speed to optimize weld quality and performance.
- Welding Gun: The welding gun holds the consumable wire electrode and directs the flow of shielding gas onto the weld joint. It also controls the welding parameters such as travel speed, electrode angle, and arc length.
- Wire Feeder: The wire feeder mechanism delivers the continuously fed consumable electrode wire from a spool to the welding gun at a controlled rate. It ensures consistent wire feed speed and smooth operation during welding.
- Gas Cylinder and Regulator: The gas cylinder contains the shielding gas, which is regulated and delivered to the welding gun through a pressure regulator. It maintains a consistent flow rate of gas to protect the weld pool from atmospheric contamination.
- Materials:
- Gas Metal Arc Welding (GMAW) is suitable for welding a wide range of metallic materials, including carbon steel, stainless steel, aluminum, copper, and other alloys.
- It is particularly well-suited for welding thin to medium thickness materials and for applications where high welding speed and efficiency are required.
- Advantages:
- High Welding Speed: Gas Metal Arc Welding (GMAW) offers high welding speeds compared to other welding processes, resulting in faster production rates and increased efficiency. It is well-suited for high-volume production and fabrication.
- Versatility: GMAW can be used to weld a wide range of materials and thicknesses, as well as dissimilar materials with different melting points. It is suitable for welding various joint configurations, including butt joints, fillet welds, lap joints, and T-joints.
- Minimal Cleanup: GMAW produces minimal spatter and fumes compared to other welding processes, resulting in a clean weld environment and reduced post-weld cleanup. It is suitable for applications where cosmetic appearance is important.
- Ease of Automation: GMAW is easily automated using robotic welding systems, allowing for precise and repeatable welds with minimal operator intervention. It is commonly used in automotive manufacturing, shipbuilding, and structural steel fabrication.
- All-Position Welding: GMAW can be performed in all welding positions, including flat, horizontal, vertical, and overhead, offering flexibility and adaptability to different joint configurations and workpiece orientations.
- Applications:
- Automotive Manufacturing: Gas Metal Arc Welding (GMAW) is widely used in the automotive industry for welding vehicle body panels, chassis components, exhaust systems, and structural assemblies. It offers high-speed welding, excellent penetration, and good weld appearance.
- Structural Steel Fabrication: GMAW is employed in the construction and fabrication of buildings, bridges, and infrastructure for welding structural components such as beams, columns, trusses, and girders. It provides strong, durable welds with high productivity.
- Shipbuilding and Marine Engineering: GMAW is utilized in shipbuilding and marine engineering for welding hulls, decks, bulkheads, and piping systems. It offers corrosion-resistant welds with good mechanical properties for maritime applications.
- Aerospace and Aviation: GMAW is used in the aerospace industry for welding aircraft structures, engine components, fuel tanks, and landing gear assemblies. It meets stringent quality and performance requirements for aerospace applications.
- Metal Fabrication: GMAW is employed in various metal fabrication industries for welding sheet metal assemblies, enclosures, and components. It offers efficient and cost-effective welding solutions for custom fabrication projects.
In summary, Gas Metal Arc Welding (GMAW), also known as MIG welding, is a versatile and widely used welding process that offers high welding speed, versatility, and ease of automation. Its applications span various industries, including automotive, structural steel fabrication, shipbuilding, aerospace, and metal fabrication.
Gas Tungsten Arc Welding (GTAW), also known as TIG welding:
Gas Tungsten Arc Welding (GTAW), commonly referred to as TIG (Tungsten Inert Gas) welding, is a versatile welding process that uses a non-consumable tungsten electrode to create the arc and join metal components together. GTAW is known for its precise control, high-quality welds, and ability to weld a wide range of materials.
- Principle of Operation:
- Gas Tungsten Arc Welding (GTAW) operates on the principle of creating an electric arc between a non-consumable tungsten electrode and the workpiece. The arc generates intense heat, melting the base metal and forming a weld pool.
- A shielding gas, such as argon, helium, or a mixture of gases, is continuously fed through the welding torch to protect the weld pool from atmospheric contamination. The gas also helps to stabilize the arc and improve weld quality.
- GTAW can be performed with or without filler metal, depending on the welding application and joint configuration. Filler metal, if used, is added manually to the weld joint as needed to fill gaps and build up the weld bead.
- Equipment:
- Welding Power Source: The welding power source provides the electrical energy necessary to create and maintain the welding arc. It controls welding parameters such as voltage, current, and pulse frequency to optimize weld quality and performance.
- TIG Welding Torch: The TIG welding torch holds the non-consumable tungsten electrode and directs the flow of shielding gas onto the weld joint. It also controls the welding parameters such as travel speed, electrode angle, and arc length.
- Tungsten Electrode: The tungsten electrode is the key component of the process and serves as the arc initiator and conductor. It is made of pure tungsten or a tungsten alloy and must be properly shaped and sharpened for optimal arc stability and weld quality.
- Gas Cylinder and Regulator: The gas cylinder contains the shielding gas, which is regulated and delivered to the TIG welding torch through a pressure regulator. It maintains a consistent flow rate of gas to protect the weld pool from atmospheric contamination.
- Materials:
- Gas Tungsten Arc Welding (GTAW) is suitable for welding a wide range of metallic materials, including carbon steel, stainless steel, aluminum, copper, titanium, and other alloys.
- It is particularly well-suited for welding thin materials and for applications where precise control, minimal heat input, and high-quality welds are required.
- Advantages:
- Precise Control: Gas Tungsten Arc Welding (GTAW) offers precise control over the welding process, allowing for accurate positioning, arc length, and heat input. It is capable of producing high-quality welds with excellent bead appearance and fusion.
- High-Quality Welds: GTAW produces clean, porosity-free welds with minimal spatter and distortion, resulting in superior mechanical properties and corrosion resistance. It is suitable for applications where weld quality is critical, such as aerospace, nuclear, and pressure vessel fabrication.
- Versatility: GTAW can be used to weld a wide range of materials and thicknesses, including dissimilar materials with different melting points. It is suitable for welding various joint configurations, including butt joints, fillet welds, lap joints, and T-joints.
- All-Position Welding: GTAW can be performed in all welding positions, including flat, horizontal, vertical, and overhead, offering flexibility and adaptability to different joint configurations and workpiece orientations.
- Tungsten Inert Gas: The use of inert shielding gases in GTAW reduces the risk of weld contamination and eliminates the need for fluxes or other consumables. It creates a clean and stable welding environment, resulting in high-quality, defect-free welds.
- Applications:
- Aerospace Manufacturing: Gas Tungsten Arc Welding (GTAW) is widely used in the aerospace industry for welding aircraft structures, engine components, fuel tanks, and exhaust systems. It offers high-quality welds with excellent strength and fatigue resistance.
- Nuclear Power Generation: GTAW is utilized in the nuclear power generation industry for welding reactor components, pressure vessels, steam generators, and piping systems. It meets stringent quality and performance requirements for nuclear applications.
- Pharmaceutical and Food Processing: GTAW is employed in the pharmaceutical and food processing industries for welding stainless steel equipment, tanks, and piping systems. It provides clean, sanitary welds with no contamination or discoloration.
- Precision Instrumentation: GTAW is used in precision instrumentation and laboratory equipment manufacturing for welding sensors, probes, and analytical instruments. It offers high-precision welds with minimal heat input and distortion.
- Artistic and Decorative Welding: GTAW is employed by artists and craftsmen for welding decorative sculptures, architectural elements, and ornamental metalwork. It allows for intricate weld designs and precise control over weld appearance.
In summary, Gas Tungsten Arc Welding (GTAW), also known as TIG welding, is a versatile and high-quality welding process that offers precise control, high-quality welds, and versatility in materials and applications. Its applications span various industries, including aerospace, nuclear, pharmaceutical, precision instrumentation, and artistic welding.
Submerged Arc Welding (SAW):
Submerged Arc Welding (SAW) is a welding process that utilizes a continuously fed electrode and a layer of granular flux to create a molten weld pool. SAW is commonly used for welding thick sections of ferrous materials in a single pass, offering high deposition rates and excellent penetration.
- Principle of Operation:
- Submerged Arc Welding (SAW) operates on the principle of creating an electric arc between a continuously fed bare electrode wire and the workpiece. The arc is submerged beneath a layer of granular flux, which shields the weld pool from atmospheric contamination and prevents spatter.
- The heat generated by the arc melts both the electrode wire and the base metal, forming a molten weld pool. The granular flux layer melts and forms a slag, which floats on the surface of the weld pool, protecting it from oxidation and facilitating weld cooling.
- SAW can be performed with or without filler metal, depending on the welding application and joint configuration. Filler metal, if used, is added manually to the weld joint as needed to fill gaps and build up the weld bead.
- Equipment:
- Welding Power Source: The welding power source provides the electrical energy necessary to create and maintain the welding arc. It controls welding parameters such as voltage, current, and travel speed to optimize weld quality and performance.
- SAW Head: The SAW head holds the electrode wire and guides it into the weld joint. It also directs the flow of granular flux onto the weld zone and provides support for the welding process.
- Electrode Wire: The electrode wire is continuously fed from a spool through the SAW head and into the weld joint. It is typically made of mild steel, low-alloy steel, or stainless steel, depending on the material being welded and the application requirements.
- Granular Flux: The granular flux is distributed over the weld joint and submerged beneath the arc during welding. It serves multiple purposes, including shielding the weld pool, controlling weld penetration, and forming a protective slag layer.
- Materials:
- Submerged Arc Welding (SAW) is primarily used for welding thick sections of ferrous materials, including carbon steel, low-alloy steel, stainless steel, and nickel-based alloys.
- It is particularly well-suited for welding heavy plate and structural components in industries such as shipbuilding, pressure vessel fabrication, and bridge construction.
- Advantages:
- High Deposition Rates: Submerged Arc Welding (SAW) offers high deposition rates compared to other welding processes, resulting in faster production rates and increased efficiency. It is capable of welding thick sections in a single pass, reducing welding time and cost.
- Deep Penetration: SAW provides excellent penetration into the base metal, resulting in strong, fully penetrated welds with good fusion and mechanical properties. It is suitable for welding thick materials and for applications requiring high joint integrity.
- Minimal Spatter: SAW produces minimal spatter and fumes compared to other welding processes, resulting in a clean weld environment and reduced post-weld cleanup. It is suitable for applications where weld appearance is important.
- Versatility: SAW can be used to weld a wide range of materials and thicknesses, as well as various joint configurations, including butt joints, fillet welds, and lap joints. It is suitable for both flat and horizontal welding positions.
- Automatic Welding: SAW is easily automated using mechanized or robotic welding systems, allowing for precise and repeatable welds with minimal operator intervention. It is commonly used in heavy fabrication and manufacturing industries.
- Applications:
- Shipbuilding and Marine Engineering: Submerged Arc Welding (SAW) is widely used in the shipbuilding industry for welding hulls, decks, bulkheads, and structural components. It offers high-speed welding, excellent penetration, and good mechanical properties for maritime applications.
- Pressure Vessel Fabrication: SAW is utilized in the fabrication of pressure vessels, boilers, and storage tanks for the petrochemical, oil and gas, and power generation industries. It provides strong, leak-tight welds with high joint integrity and reliability.
- Bridge Construction: SAW is employed in the construction of bridges and infrastructure for welding bridge girders, beams, and trusses. It offers high-strength welds with excellent fatigue resistance and durability in harsh environmental conditions.
- Heavy Fabrication: SAW is used in heavy fabrication industries for welding structural steel components, crane booms, and machinery frames. It offers high deposition rates and deep penetration, reducing welding time and cost for large-scale projects.
- Railway Construction: SAW is employed in railway construction and maintenance for welding rail tracks, switches, and crossings. It provides strong, durable welds with good impact resistance and dimensional stability for railway infrastructure.
In summary, Submerged Arc Welding (SAW) is a versatile and efficient welding process that offers high deposition rates, deep penetration, and minimal spatter. Its applications span various industries, including shipbuilding, pressure vessel fabrication, bridge construction, heavy fabrication, and railway construction.
Shielded Metal Arc Welding (SMAW), also known as Stick Welding:
Shielded Metal Arc Welding (SMAW), commonly referred to as Stick Welding, is a manual arc welding process that uses a consumable electrode coated with a flux to create the arc and join metal components together. SMAW is widely used for its versatility, portability, and ability to weld a variety of materials in various positions.
- Principle of Operation:
- Shielded Metal Arc Welding (SMAW) operates on the principle of creating an electric arc between a consumable coated electrode and the workpiece. The arc generates intense heat, melting both the electrode and the base metal, forming a molten weld pool.
- The flux coating on the electrode melts and forms a protective slag over the weld pool, shielding it from atmospheric contamination and preventing spatter. The slag also helps to stabilize the arc and improve weld quality.
- SMAW can be performed with or without filler metal, depending on the welding application and joint configuration. Filler metal, if used, is provided by the electrode itself as it melts into the weld pool.
- Equipment:
- Welding Power Source: The welding power source provides the electrical energy necessary to create and maintain the welding arc. It controls welding parameters such as voltage, current, and arc length to optimize weld quality and performance.
- Welding Electrodes: The welding electrodes are consumable metal rods coated with a flux material. They are available in various types and sizes to suit different welding applications and materials. The flux coating provides arc stability, slag formation, and shielding gas protection.
- Electrode Holder: The electrode holder, also known as the stinger or electrode clamp, holds the welding electrode and conducts the welding current to the electrode tip. It provides a comfortable grip for the welder and allows for precise electrode manipulation during welding.
- Ground Clamp: The ground clamp connects the workpiece to the welding power source and completes the electrical circuit. It ensures proper electrical grounding and helps to maintain welding stability and safety.
- Materials:
- Shielded Metal Arc Welding (SMAW) is suitable for welding a wide range of materials, including carbon steel, stainless steel, cast iron, nickel alloys, and non-ferrous metals.
- It is particularly well-suited for welding materials with surface contaminants or rust, as the flux coating on the electrode helps to remove impurities and provide a clean weld.
- Advantages:
- Versatility: Shielded Metal Arc Welding (SMAW) is a versatile welding process that can be used to weld a wide range of materials and thicknesses. It is suitable for welding in various positions, including flat, horizontal, vertical, and overhead.
- Portability: SMAW equipment is compact and portable, making it well-suited for on-site welding and repair work where access to a power source may be limited. It does not require external shielding gas, making it suitable for outdoor applications.
- All-Position Welding: SMAW can be performed in all welding positions, offering flexibility and adaptability to different joint configurations and workpiece orientations. It is commonly used in construction, fabrication, and maintenance applications.
- Minimal Equipment Requirements: SMAW equipment is simple and straightforward, consisting of a welding power source, electrodes, electrode holder, and ground clamp. It is easy to set up and operate, requiring minimal training and maintenance.
- Cost-Effective: SMAW is a cost-effective welding process that requires relatively low initial investment and operating costs compared to other welding processes. It is suitable for small-scale projects, repairs, and maintenance work.
- Applications:
- Construction and Fabrication: Shielded Metal Arc Welding (SMAW) is widely used in construction and fabrication industries for welding structural steel, pipelines, bridges, and buildings. It offers versatility, portability, and ease of use for on-site welding applications.
- Maintenance and Repair: SMAW is employed in maintenance and repair work for welding equipment, machinery, vehicles, and infrastructure. It is suitable for repairing worn or damaged components and for performing field repairs in remote locations.
- Shipbuilding and Marine Repair: SMAW is utilized in the shipbuilding and marine repair industries for welding hulls, decks, bulkheads, and piping systems. It provides reliable, high-quality welds with good penetration and mechanical properties.
- Automotive and Transportation: SMAW is used in the automotive and transportation industries for welding frames, chassis components, and exhaust systems. It offers versatility and durability for welding various materials and thicknesses.
- Agriculture and Heavy Equipment: SMAW is employed in agriculture and heavy equipment manufacturing for welding farm machinery, construction equipment, and mining machinery. It provides strong, durable welds for heavy-duty applications.
In summary, Shielded Metal Arc Welding (SMAW), also known as Stick Welding, is a versatile and widely used welding process that offers versatility, portability, and ease of use. Its applications span various industries, including construction, fabrication, maintenance, shipbuilding, automotive, agriculture, and heavy equipment manufacturing.
Flux-Cored Arc Welding (FCAW):
Flux-Cored Arc Welding (FCAW) is a semi-automatic or automatic arc welding process that uses a tubular wire electrode filled with flux to create the arc and join metal components together. FCAW is known for its high deposition rates, deep penetration, and ability to weld thick materials in various positions.
- Principle of Operation:
- Flux-Cored Arc Welding (FCAW) operates on the principle of creating an electric arc between a continuously fed tubular wire electrode and the workpiece. The arc generates intense heat, melting both the electrode and the base metal, forming a molten weld pool.
- The flux contained within the electrode wire melts and forms a protective slag over the weld pool, shielding it from atmospheric contamination and preventing spatter. The slag also helps to stabilize the arc and improve weld quality.
- FCAW can be performed with or without external shielding gas, depending on the type of electrode used. Gas-shielded FCAW uses a shielding gas, typically a mixture of CO2 and argon, while self-shielded FCAW relies on the flux contained within the electrode wire for shielding.
- Equipment:
- Welding Power Source: The welding power source provides the electrical energy necessary to create and maintain the welding arc. It controls welding parameters such as voltage, current, and wire feed speed to optimize weld quality and performance.
- FCAW Gun: The FCAW gun holds the tubular wire electrode and guides it into the weld joint. It also directs the flow of shielding gas, if used, onto the weld zone and provides support for the welding process.
- Wire Feeder: The wire feeder mechanism delivers the continuously fed tubular wire electrode from a spool to the FCAW gun at a controlled rate. It ensures consistent wire feed speed and smooth operation during welding.
- Gas Cylinder and Regulator (for gas-shielded FCAW): The gas cylinder contains the shielding gas, which is regulated and delivered to the FCAW gun through a pressure regulator. It maintains a consistent flow rate of gas to protect the weld pool from atmospheric contamination.
- Materials:
- Flux-Cored Arc Welding (FCAW) is suitable for welding a wide range of materials, including carbon steel, low-alloy steel, stainless steel, and nickel alloys.
- It is particularly well-suited for welding thick materials and for applications requiring high deposition rates and deep penetration.
- Advantages:
- High Deposition Rates: Flux-Cored Arc Welding (FCAW) offers high deposition rates compared to other welding processes, resulting in faster production rates and increased efficiency. It is capable of welding thick sections in a single pass, reducing welding time and cost.
- Deep Penetration: FCAW provides excellent penetration into the base metal, resulting in strong, fully penetrated welds with good fusion and mechanical properties. It is suitable for welding thick materials and for applications requiring high joint integrity.
- All-Position Welding: FCAW can be performed in all welding positions, including flat, horizontal, vertical, and overhead, offering flexibility and adaptability to different joint configurations and workpiece orientations.
- Minimal Cleanup: FCAW produces minimal spatter and fumes compared to other welding processes, resulting in a clean weld environment and reduced post-weld cleanup. It is suitable for applications where weld appearance is important.
- Versatility: FCAW can be used with a variety of electrode types and flux formulations to suit different welding applications and materials. It offers versatility and flexibility in welding various joint configurations and workpiece thicknesses.
- Applications:
- Heavy Fabrication: Flux-Cored Arc Welding (FCAW) is widely used in heavy fabrication industries for welding structural steel components, pressure vessels, and machinery. It offers high deposition rates and deep penetration for welding thick materials.
- Shipbuilding and Marine Engineering: FCAW is utilized in the shipbuilding and marine engineering industries for welding hulls, decks, bulkheads, and piping systems. It provides reliable, high-quality welds with good penetration and mechanical properties.
- Construction and Infrastructure: FCAW is employed in construction and infrastructure projects for welding bridges, buildings, and structural components. It offers versatility and efficiency for on-site welding applications.
- Pipeline Construction: FCAW is used in pipeline construction for welding large-diameter pipelines and pipe joints. It offers high-speed welding and good penetration for joining long sections of pipe in various positions.
- Oil and Gas Industry: FCAW is employed in the oil and gas industry for welding storage tanks, pressure vessels, and pipeline infrastructure. It provides strong, durable welds with excellent corrosion resistance for harsh environments.
In summary, Flux-Cored Arc Welding (FCAW) is a versatile and efficient welding process that offers high deposition rates, deep penetration, and all-position welding capabilities. Its applications span various industries, including heavy fabrication, shipbuilding, construction, pipeline, and oil and gas.
Electrogas Welding (EGW):
Electrogas Welding (EGW) is a semi-automatic arc welding process used primarily for welding thick steel plates in a vertical position. It is a variation of the flux-cored arc welding (FCAW) process but is specifically designed for vertical-up welding applications.
- Principle of Operation:
- Electrogas Welding (EGW) operates on the principle of creating an electric arc between a continuously fed consumable electrode and the workpiece. The arc generates intense heat, melting both the electrode and the base metal, forming a molten weld pool.
- Unlike traditional FCAW, EGW employs a vertical-up welding technique, where the welding torch is positioned above the joint, and the weld pool travels upward as the welding progresses.
- The welding process is typically performed with a single-pass technique, where the electrode is continuously fed into the joint, and the weld pool solidifies behind the arc.
- Equipment:
- Welding Power Source: The welding power source provides the electrical energy necessary to create and maintain the welding arc. It controls welding parameters such as voltage, current, and wire feed speed to optimize weld quality and performance.
- EGW Head: The EGW head holds the consumable electrode and guides it into the weld joint. It also directs the flow of shielding gas, typically a mixture of CO2 and argon, onto the weld zone to protect it from atmospheric contamination.
- Wire Feeder: The wire feeder mechanism delivers the continuously fed consumable electrode from a spool to the EGW head at a controlled rate. It ensures consistent wire feed speed and smooth operation during welding.
- Materials:
- Electrogas Welding (EGW) is primarily used for welding thick steel plates, typically ranging from 12 mm to several inches in thickness.
- It is commonly used in heavy fabrication industries for welding ship hulls, pressure vessels, storage tanks, and structural components.
- Advantages:
- High Productivity: Electrogas Welding (EGW) offers high deposition rates and fast welding speeds compared to other welding processes. It is capable of welding thick sections in a single pass, reducing welding time and labor costs.
- Deep Penetration: EGW provides excellent penetration into the base metal, resulting in strong, fully penetrated welds with good fusion and mechanical properties. It is suitable for welding thick materials and for applications requiring high joint integrity.
- Vertical-Up Welding: EGW is specifically designed for vertical-up welding applications, where the weld pool travels upward against gravity. This technique allows for better control of weld penetration and reduces the risk of weld defects.
- Minimal Distortion: EGW produces minimal distortion and heat-affected zone compared to other welding processes, resulting in straighter and more uniform welds. It is suitable for welding large and heavy components without significant distortion.
- Versatility: EGW can be used with a variety of consumable electrodes and shielding gas mixtures to suit different welding applications and materials. It offers versatility and flexibility in welding various joint configurations and workpiece thicknesses.
- Applications:
- Shipbuilding and Marine Engineering: Electrogas Welding (EGW) is widely used in the shipbuilding and marine engineering industries for welding ship hulls, bulkheads, and decks. It offers high-speed welding and good penetration for joining thick steel plates.
- Pressure Vessel Fabrication: EGW is employed in the fabrication of pressure vessels, storage tanks, and boilers for the petrochemical, oil and gas, and power generation industries. It provides strong, leak-tight welds with high joint integrity.
- Heavy Fabrication: EGW is used in heavy fabrication industries for welding structural steel components, bridge girders, and machinery. It offers high productivity and efficiency for welding thick sections in a single pass.
- Infrastructure Construction: EGW is employed in construction projects for welding large structural components, such as bridge piers, columns, and beams. It offers fast welding speeds and minimal distortion for vertical-up welding applications.
- Offshore Construction: EGW is used in offshore construction projects for welding offshore platforms, jackets, and pipelines. It provides reliable, high-quality welds with good penetration and mechanical properties for marine environments.
In summary, Electrogas Welding (EGW) is a high-productivity arc welding process specifically designed for vertical-up welding applications on thick steel plates. Its applications span various industries, including shipbuilding, pressure vessel fabrication, heavy fabrication, infrastructure construction, and offshore construction.
Atomic Hydrogen Welding (AHW):
Atomic Hydrogen Welding (AHW) is a welding process that utilizes the heat generated by the reaction between hydrogen molecules dissociated into atomic hydrogen to create a high-temperature welding arc. AHW was developed in the early 20th century but has since been largely replaced by more modern welding processes.
- Principle of Operation:
- Atomic Hydrogen Welding (AHW) operates on the principle of creating an electric arc between two tungsten electrodes in a hydrogen atmosphere. The hydrogen gas is first passed through a heated chamber to dissociate the molecules into atomic hydrogen, which is highly reactive.
- When an electric arc is struck between the tungsten electrodes, the atomic hydrogen combines explosively at the arc, releasing a large amount of heat energy. This heat is used to melt and fuse the base metal, forming a weld bead.
- AHW can be performed with or without filler metal, depending on the welding application and joint configuration. Filler metal, if used, is added manually to the weld joint as needed to fill gaps and build up the weld bead.
- Equipment:
- AHW Torch: The AHW torch consists of two tungsten electrodes separated by a small gap, through which the hydrogen gas flows. The torch is designed to maintain a stable arc and provide precise control over the welding process.
- Hydrogen Gas Supply: The hydrogen gas supply provides the fuel for the AHW process. The gas is typically stored in compressed gas cylinders and regulated to the desired flow rate using pressure regulators.
- Power Source: The power source supplies the electrical energy necessary to create and maintain the welding arc. It controls welding parameters such as voltage, current, and arc length to optimize weld quality and performance.
- Materials:
- Atomic Hydrogen Welding (AHW) is primarily used for welding high-purity metals, such as tungsten, titanium, and some stainless steels.
- It is particularly well-suited for welding refractory metals and alloys with high melting points, as the high-temperature arc generated by AHW can effectively melt and fuse these materials.
- Advantages:
- High Heat Input: Atomic Hydrogen Welding (AHW) produces a high-temperature welding arc capable of melting and fusing refractory metals and alloys with high melting points. It is suitable for welding materials that are difficult to weld using conventional welding processes.
- Minimal Contamination: AHW operates in a hydrogen atmosphere, which minimizes the risk of atmospheric contamination and weld defects. The absence of atmospheric gases such as oxygen and nitrogen helps to produce clean, high-quality welds.
- High Welding Speeds: AHW can achieve high welding speeds compared to other welding processes, resulting in faster production rates and increased efficiency. It is suitable for applications where rapid welding is required.
- Precise Control: AHW offers precise control over the welding process, allowing for accurate positioning of the welding arc and precise heat input to the weld zone. It is suitable for welding thin materials and for applications requiring tight tolerances.
- Versatility: AHW can be used to weld a wide range of materials, including refractory metals, high-strength alloys, and dissimilar metals. It offers versatility and flexibility in welding various joint configurations and workpiece thicknesses.
- Applications:
- Aerospace and Defense: Atomic Hydrogen Welding (AHW) is used in the aerospace and defense industries for welding critical components, such as rocket engine parts, turbine blades, and heat exchangers. It offers high weld quality and reliability for mission-critical applications.
- Electronics and Semiconductor Manufacturing: AHW is employed in electronics and semiconductor manufacturing for welding precision components, such as microelectronic devices, sensors, and vacuum chambers. It provides clean, high-purity welds with minimal contamination.
- Research and Development: AHW is used in research and development laboratories for welding experimental materials and prototypes. It offers precise control over the welding process and the ability to weld materials with unique properties.
- Specialty Welding Applications: AHW is employed in specialty welding applications where high-temperature welding arcs are required, such as welding refractory metals, superalloys, and exotic materials. It offers a unique combination of high heat input and minimal contamination.
In summary, Atomic Hydrogen Welding (AHW) is a specialized welding process that utilizes the heat generated by the reaction between hydrogen molecules dissociated into atomic hydrogen to create a high-temperature welding arc. Its applications span various industries, including aerospace, defense, electronics, semiconductor manufacturing, research, and specialty welding.
Electroslag Welding (ESW):
Electroslag Welding (ESW) is a highly efficient welding process used primarily for welding thick steel plates in a vertical position. It is characterized by its high deposition rates, deep penetration capabilities, and ability to produce single-pass welds on thick materials.
- Principle of Operation:
- Electroslag Welding (ESW) operates on the principle of creating an electric arc between a continuously fed consumable electrode and the workpiece. The arc generates intense heat, melting both the electrode and the base metal, forming a molten weld pool.
- As the arc heats the base metal, a layer of flux material is added to the weld zone, typically in the form of granular flux or a flux-cored electrode. The flux serves multiple purposes, including shielding the weld pool from atmospheric contamination, controlling weld penetration, and providing support for the molten metal.
- Electroslag welding is characterized by the use of a molten slag layer that covers the entire weld pool, creating a highly efficient environment for welding thick materials in a single pass.
- Equipment:
- Welding Power Source: The welding power source provides the electrical energy necessary to create and maintain the welding arc. It controls welding parameters such as voltage, current, and electrode travel speed to optimize weld quality and performance.
- Electroslag Welding Head: The ESW head holds the consumable electrode and guides it into the weld joint. It also directs the flow of flux material onto the weld zone and provides support for the welding process.
- Flux Delivery System: The flux delivery system delivers the flux material to the weld zone, where it forms a molten slag layer over the weld pool. It ensures consistent flux coverage and distribution to optimize weld quality and performance.
- Materials:
- Electroslag Welding (ESW) is primarily used for welding thick steel plates, typically ranging from 25 mm to several meters in thickness.
- It is commonly used in heavy fabrication industries for welding ship hulls, pressure vessels, storage tanks, and structural components.
- Advantages:
- High Deposition Rates: Electroslag Welding (ESW) offers extremely high deposition rates compared to other welding processes, resulting in faster production rates and increased efficiency. It is capable of welding thick sections in a single pass, reducing welding time and labor costs.
- Deep Penetration: ESW provides exceptional penetration into the base metal, resulting in strong, fully penetrated welds with good fusion and mechanical properties. It is suitable for welding thick materials and for applications requiring high joint integrity.
- Single-Pass Welding: Electroslag welding can often produce single-pass welds on materials several inches thick, reducing the need for multiple welding passes and minimizing the risk of weld defects.
- Minimal Distortion: ESW produces minimal distortion and heat-affected zone compared to other welding processes, resulting in straighter and more uniform welds. It is suitable for welding large and heavy components without significant distortion.
- Versatility: ESW can be used to weld a wide range of materials, including carbon steel, low-alloy steel, stainless steel, and nickel alloys. It offers versatility and flexibility in welding various joint configurations and workpiece thicknesses.
- Applications:
- Shipbuilding and Marine Engineering: Electroslag Welding (ESW) is widely used in the shipbuilding and marine engineering industries for welding ship hulls, bulkheads, and decks. It offers high-speed welding and good penetration for joining thick steel plates.
- Pressure Vessel Fabrication: ESW is employed in the fabrication of pressure vessels, storage tanks, and boilers for the petrochemical, oil and gas, and power generation industries. It provides strong, leak-tight welds with high joint integrity.
- Heavy Fabrication: ESW is used in heavy fabrication industries for welding structural steel components, bridge girders, and machinery. It offers high productivity and efficiency for welding thick sections in a single pass.
- Infrastructure Construction: ESW is employed in construction projects for welding large structural components, such as bridge piers, columns, and beams. It offers fast welding speeds and minimal distortion for vertical-up welding applications.
- Offshore Construction: ESW is used in offshore construction projects for welding offshore platforms, jackets, and pipelines. It provides reliable, high-quality welds with good penetration and mechanical properties for marine environments.
In summary, Electroslag Welding (ESW) is a highly efficient welding process that offers high deposition rates, deep penetration capabilities, and the ability to produce single-pass welds on thick materials. Its applications span various industries, including shipbuilding, pressure vessel fabrication, heavy fabrication, infrastructure construction, and offshore construction.
EMS Metalworking Machinery
We design, manufacture and assembly metalworking machinery such as:
- Hydraulic transfer press
- Glass mosaic press
- Hydraulic deep drawing press
- Casting press
- Hydraulic cold forming press
- Hydroforming press
- Composite press
- Silicone rubber moulding press
- Brake pad press
- Melamine press
- SMC & BMC Press
- Labrotaroy press
- Edge cutting trimming machine
- Edge curling machine
- Trimming beading machine
- Trimming joggling machine
- Cookware production line
- Pipe bending machine
- Profile bending machine
- Bandsaw for metal
- Cylindrical welding machine
- Horizontal pres and cookware
- Kitchenware, hotelware
- Bakeware and cuttlery production machinery
as a complete line as well as an individual machine such as:
- Edge cutting trimming beading machines
- Polishing and grinding machines for pot and pans
- Hydraulic drawing presses
- Circle blanking machines
- Riveting machine
- Hole punching machines
- Press feeding machine
You can check our machinery at work at: EMS Metalworking Machinery – YouTube
- Beading and ribbing
- Flanging
- Trimming
- Curling
- Lock-seaming
- Ribbing
- Flange-punching